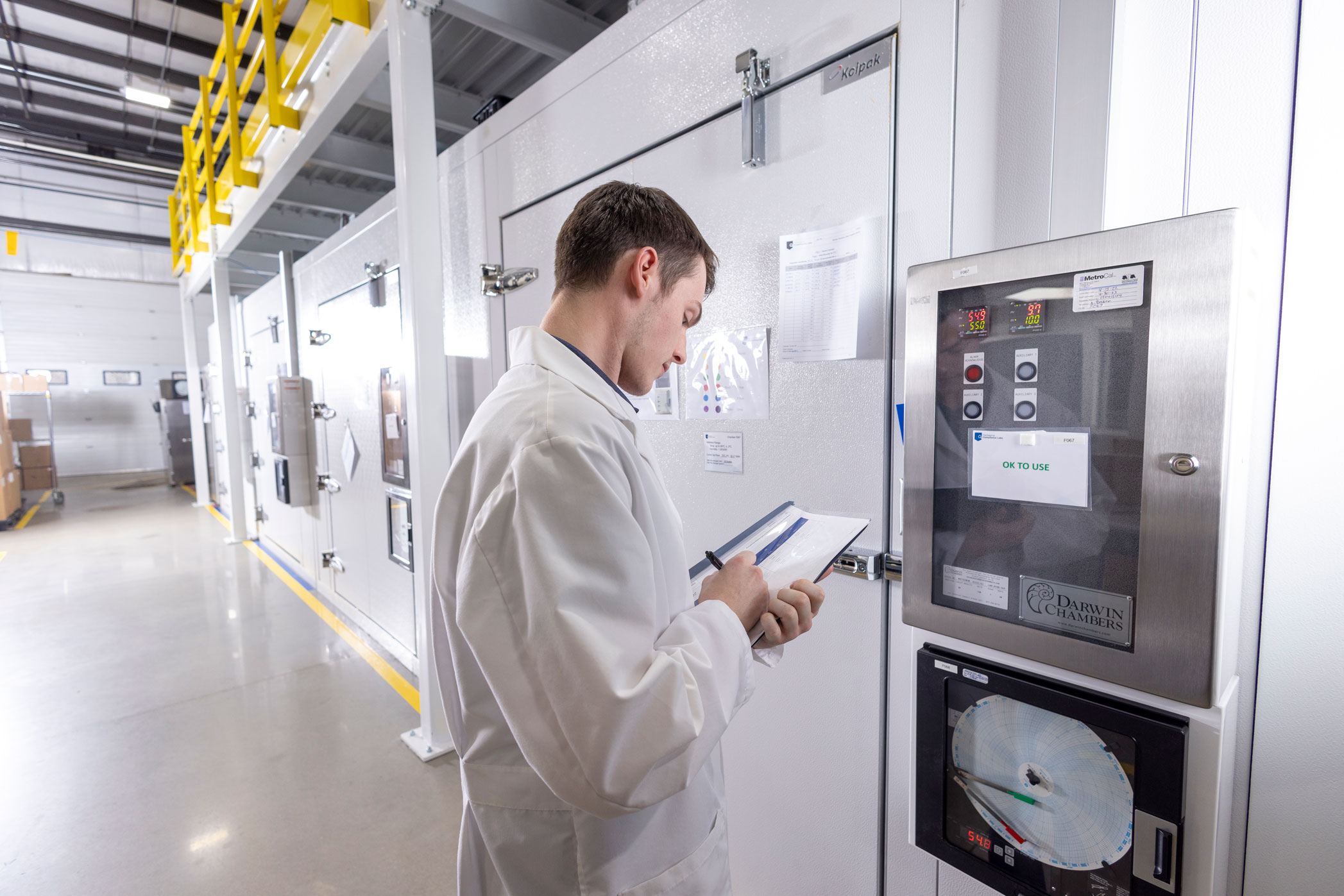
ASTM Accelerated Aging Testing
ISO 11607 Part 1 requires shelf life studies to demonstrate that sterile barrier packaging systems are capable of maintaining sterile barrier integrity through claimed expiration dates. While the FDA does require real-time shelf life studies to be undertaken, they will allow product to be approved for sale on the market sooner based on the results of accelerated shelf life studies.
PCL provides ASTM F1980 testing to evaluate the long-term effects on packaging in a compressed timeline. The results of accelerated aging testing are used to support shelf-life claims until data becomes available from real time aging studies.
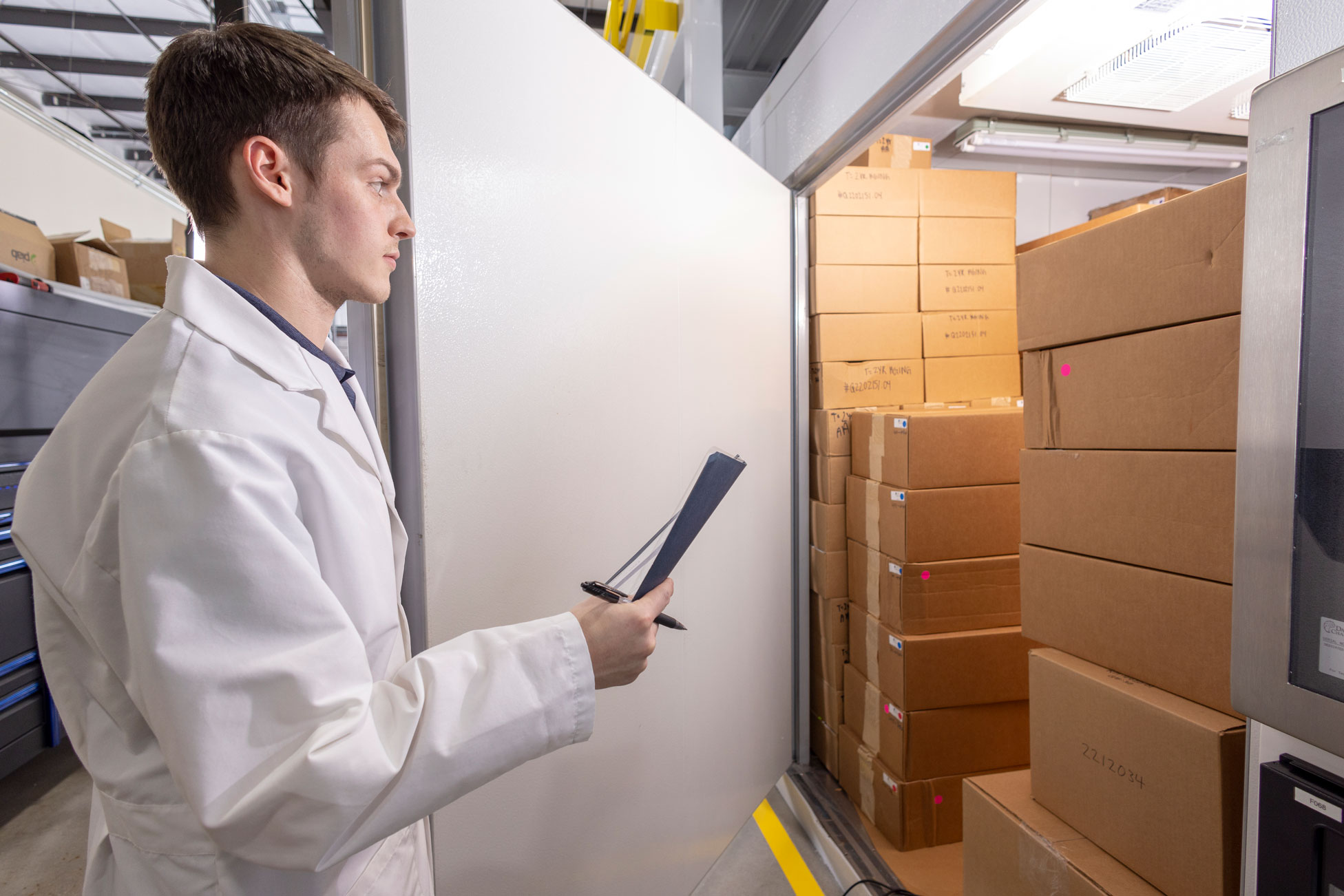
Industry Application
Accelerated Aging per ASTM F1980 is a standard that provides guidance for how to develop accelerated aging protocols. Accelerated aging works by putting samples in a chamber and applying heat and/or humidity for a predetermined amount of time, usually weeks or months. For example, the most common temperature used in sterile barrier packaging validation is 55 °C. Assuming standard considerations of the real-world storage environment, then it will only take 40 days in hot conditioning to simulate a full 365 days (1 year) of real-world storage time.
If medical device manufacturers had to wait for their real-time aging data before they could go to market with their shelf life claim, there would be a drastic halt in medical device innovation. Therefore, the FDA will accept accelerated aging data for your medical device shelf life claim as long as real-time aging testing is performed in parallel to confirm accelerated aging findings.
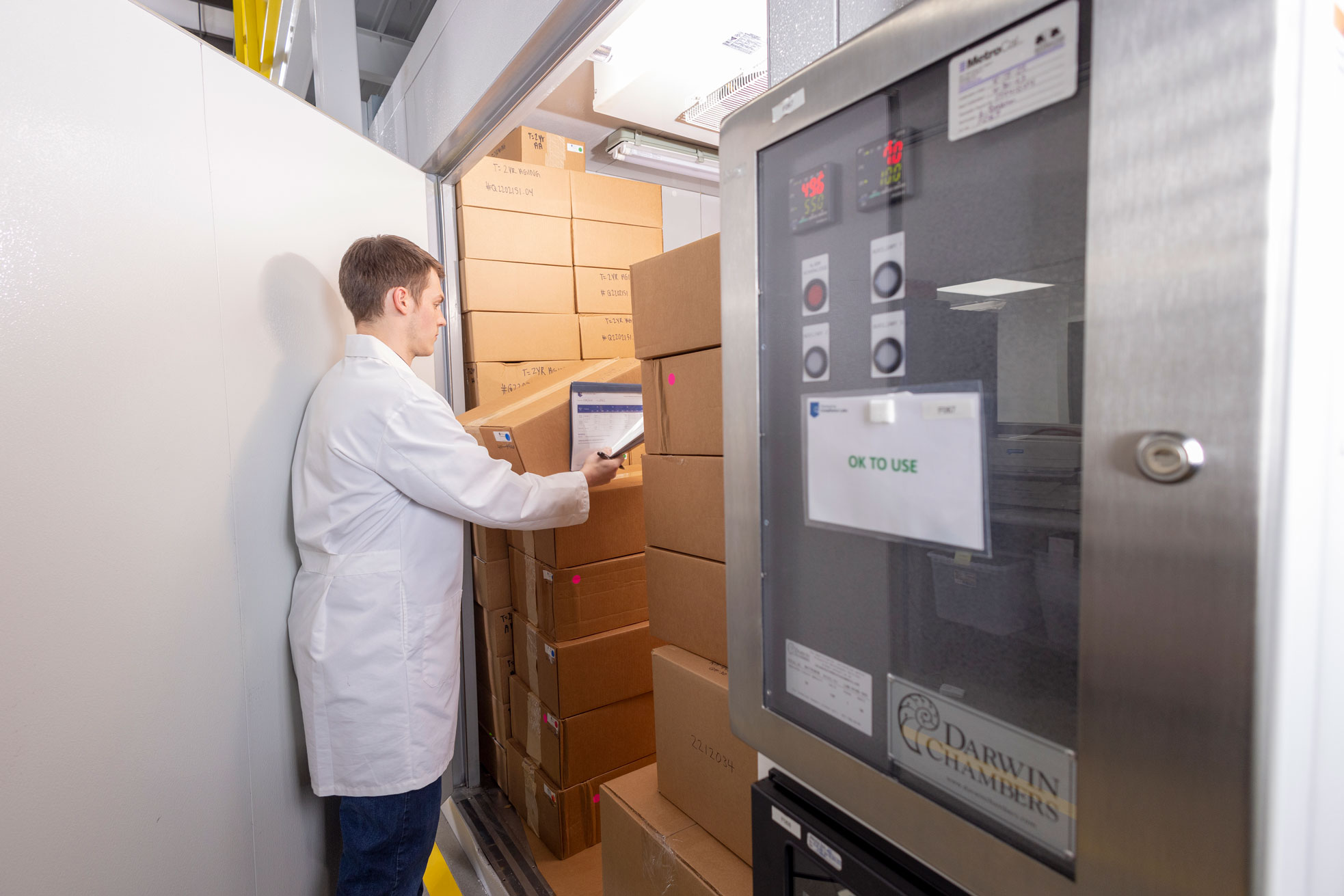
The typical temperatures used to test by most medical engineers are 50°C, 55°C, and 60°C. It is important, however, to consider the materials of construction when determining the test specifications. Our Aging Calculator is a great tool to estimate how many days your study will require. If you have questions about the accelerated aging of your sterile medical device packaging, we are ready to discuss your project to recommend the best course of action.
The Accelerated Aging Test method
Determining the conditions for an Accelerated Aging Study
Let us reflect for a moment about what the environment is like in a storage room in a healthcare setting. Healthcare storage rooms are typically air-conditioned, well lit, and are not too humid. So, why does heat come into play for accelerated aging testing? Wouldn’t increasing the heat alter the packaging in a negative way? With the help of the Arrhenius equation provided to us in ASTM F1980, we are able to determine an appropriate accelerated aging temperature to meet the needs of your project schedule while also considering the material properties of your samples.
The Arrhenius equation considers the assumed real-world storage temperature, your proposed accelerated aging temperature, the total shelf life that is being simulated, and then calculates a compressed accelerated aging timeline. At 55 degC, the most common accelerated aging temperature for sterile barrier packaging validations, one-year (365 days) of real-world storage time can be simulated in as little as 40 days in the chamber. Similarly, a five-year (1,825 days) real-world storage time can be simulated in 200 days in the chamber.
The accelerated aging calculator on our website takes all the necessary factors and gives you the output of how many days your samples will need to be in the accelerated aging chamber for.
The first equation required is the Accelerated Aging Factor (AAF). The estimate is calculated by the following equation:
To discover the accelerated aging time (AAT) needed to establish equivalence to real-time aging is determined by the following equation:
Accelerated Aging Time (AAT) = Desired (RT)/AAF
Thankfully, our calculators automate these equations these two steps for us!
Determining a temperature for Accelerated Aging
It is important that we understand the temperature for aging samples. A higher temperature will mean samples are in the chamber for less time while a lower temperature will require the samples to stay in there for longer.
Because medical device packaging material is manufactured with polymers, we cannot increase the temperature too much because the heat would alter the properties of that material to the point where the simulated circumstances become unrealistic and therefore are not a good representation of what the packaging will endure in the real-world setting. Failures associated with this are trays melting, film delaminating, or seals softening.
The goal is the find the highest temperature that we can use that is not going to affect that packaging in a negative or unrealistic way.
With all that said, 55°C is the most common temperature that we see that most packaging can endure.
Determining a humidity for Accelerated Aging
ASTM F1980 requires the user to consider if the packaging materials or the materials of the devices inside are susceptible to deterioration if exposed to moisture for an extended period of time, such as corrosion. If so, then the standard recommends conducting the accelerated aging study using 50% relative humidity. The user may still choose their desired temperature.
Frequently Asked Questions
Why is accelerated aging testing required for medical devices to go to market?
Section 8.3.1 of ISO 11607 states that “stability testing shall demonstrate that the sterile barrier system maintains integrity over time”. Section 8.3.3. of ISO 11607 also states that “Stability testing, using aging protocols, shall be regarded as sufficient evidence for claimed expiry dates until real-time aging studies are available.”
What is accelerated aging?
Accelerated aging is a theoretical calculation of how a sterile packaging system will degrade over time. Accelerated aging testing provides data that allows medical device manufacturers to go to market with their desired shelf-life claim.
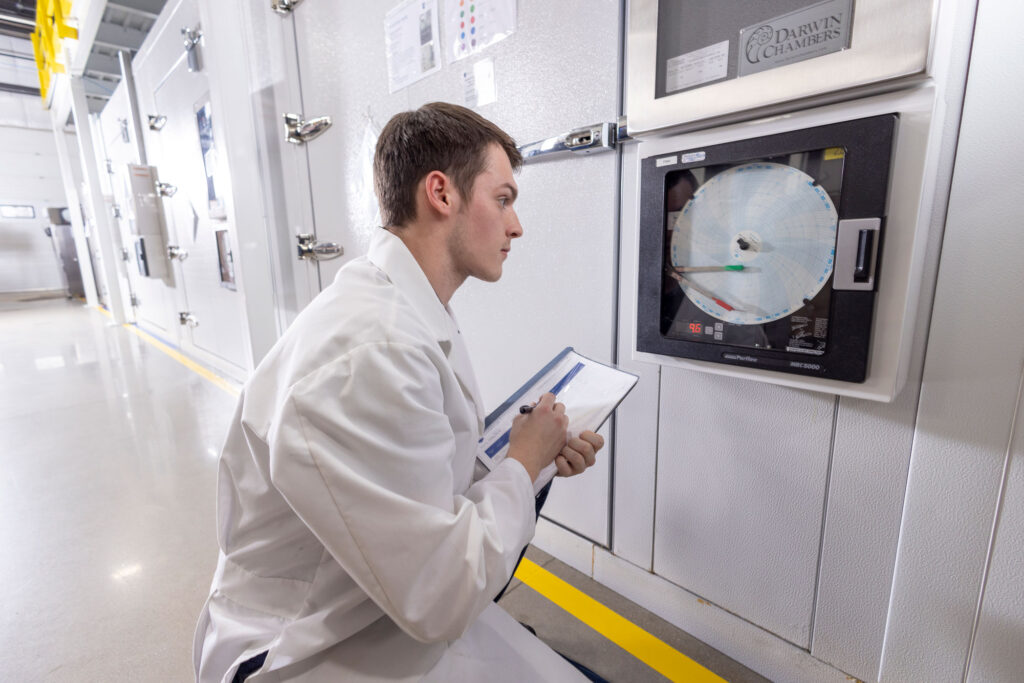