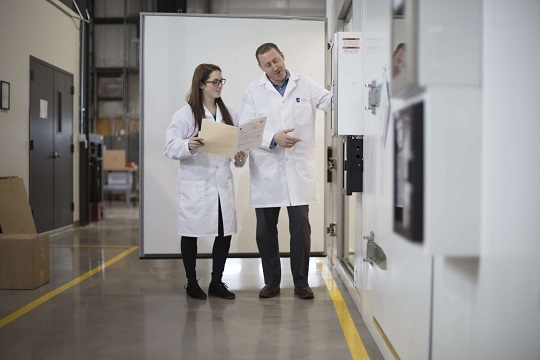
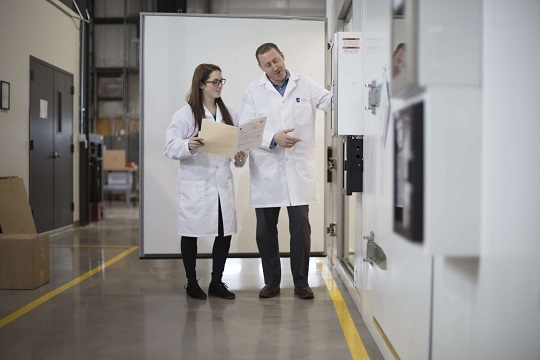
At this point, we’ve explained the first two steps of the packaging validation process. At PCL, we refer to the first step as the “Make Pillar” and the second step as the “Ship Pillar”. Next, we will explore the third step or the “Store Pillar”. This step simulates what packaging will endure in the typical real-life setting of a healthcare storage room.
Your everyday person wouldn’t think that cranking up the heat to about double of what the environment would normally be and subjecting samples to those temperatures would result in usable data to prove a packages shelf life, yet somehow it does! How? Well, it requires a little bit of math and a little bit of science. Continue reading to learn more about accelerated aging as it pertains to packaging validation per ISO 11607!
Accelerated Aging – ASTM F1980
Accelerated Aging per ASTM F1980 is a standard that provides guidance for how to develop accelerated aging protocols. Accelerated aging works by putting samples in a chamber and applying heat to them for a duration of time. This act simulates what happens to the properties that make up the packaging material over time.
If medical device manufacturers had to wait for their real-time aging data before they could go to market with their shelf life claim, there would be a drastic halt in medical device innovation. Therefore, the FDA will accept accelerated aging data for your medical device shelf life claim as long as real-time aging testing is performed in parallel. When the FDA knocks on your door when your expiration date is up, you will need real-time aging data to prove your shelf life. We will touch on real-time aging later in this article.
Determining the Conditions for an Accelerated Aging Study
Let us reflect for a moment about what the environment is like in a storage room in a healthcare setting. Healthcare storage rooms are typically air-conditioned, well lit, and are not too humid. So, why does heat come into play for accelerated aging testing? Wouldn’t increasing the heat alter the packaging in a negative way? With the help of the Arrhenius equation provided to us in ASTM F1980, we are able to find that sweet spot so we don’t cook your samples and so you’re able to learn how your sterile packaging will stand up over time.
The Arrhenius equation takes all the factors that you would consider in the real world and helps you come up with the abbreviated time point for your accelerated aging study. At the end of the day, we must understand if something is going to sit in a hospital storage room at 23°C for a year how it is going to stand up against time. Whether we put samples in the aging chamber at 50°C or 60°C, we have to know the amount of time they’ll be required to be in the accelerated aging chamber, which is what the Arrhenius equation provides us.
The accelerated aging calculator on our website takes all the necessary factors and gives you the output of how many days your samples will need to be in the accelerated aging chamber for.
The first equation required is the Accelerated Aging Factor (AAF). The estimate is calculated by the following equation:
To discover the accelerated aging time (AAT) needed to establish equivalence to real-time aging is determined by the following equation:
Accelerated Aging Time (AAT) = Desired (RT)/AAF
Thankfully, our calculators automate these equations these two steps for us!
Determining A Temperature for Accelerated Aging
It is important that we understand the temperature at which clients want to age their samples. A higher temperature will mean samples are in the chamber for less time while a lower temperature will require the samples to stay in there for longer.
By the time we get to the accelerated aging portion of a packaging validation, it is possible there have been delays and you may want to find ways to shorten the duration at which your samples are in accelerated aging. Unfortunately, we are not able to crank up the heat to shorten your study down to 5 days. For more information on how we determine accelerated aging temperature, read one of our previous blogs on the topic.
Because medical device packaging material is manufactured with polymers, we cannot increase the temperature too much because the heat would alter the properties of that material to the point where the simulated circumstances become unrealistic and therefore are not a good representation of what the packaging will endure in the real-world setting. Failures associated with this are trays melting, film delaminating, or seals softening.
The goal is the find the highest temperature that we can use that is not going to affect that packaging in a negative or unrealistic way.
With all that said, 55°C is the most common temperature that we see that most packaging can endure.
Humidity
Humidity is not a factor for determining accelerated aging duration. This is because heightened humidity can create defects that are not related to time-related stress. Anything that points to high humidity is a different type of study, more like environmental conditioning that we conduct before transit testing. To play it safe, we target to keep relative humidity (RH) levels below 20%.
If I have 20 medical devices in a product line, do the packages for each device require accelerated aging?
The short answer, no! ISO 11607 allows us to test the ‘worst case’ product if the packaging material and design are the same across the board. The worst-case could be the biggest and heaviest or smallest and most fragile product in a line. If the client is not sure which is the actual worst case, then we could test with a bookend approach, so we cover all the bases.
An example of this is if you are a hip stem manufacturer and have 20 different sizes available, we would typically test the package that holds the largest hip stem.
Integrity Testing Post Accelerated Aging
Our lab techs perform a lot of the same integrity tests after accelerated aging that they do post transit because, in essence, we are looking for the same thing – to confirm package integrity. Those tests include visual inspection, bubble leak testing, and peel strength testing.
We want to make sure the integrity of the whole package is maintained during accelerated aging, but we will still need to differentiate between what is a time-related defect versus an event-related defect. Transit testing, or distribution simulation testing, creates event-related defects, such as failures from drops or vibration testing, whereas accelerated aging studies produce time-related defects.
Time-related defects will be observed as seals delaminating, the color of packaging can change if the packaging ‘cooks’ too much, or packaging can melt if the temperature is far too high.
Once integrity testing is done and your samples pass, you can submit your accelerated aging data to the FDA and make the proposed shelf life claim for your medical device packaging until real-time aging is complete.
Real-Time Aging
As we mentioned above, accelerated aging data is acceptable to make your shelf life claim, but that shelf life claim relies on real-time aging. Once your expiration date is up, you will need to test the packages integrity for those samples to prove the shelf life claim you made for this packaging stands up against time.
At PCL, we offer Real-Time Aging storage for our clients so they do not have to manage where those samples would live in their facility. The environment where the samples are housed at our lab is human ambient conditions (high 60’s, low 70’s). Once your samples have reached their expiration date, we’ll test the samples the same way we do after accelerated aging testing and send you a report that verifies your shelf life claim!
If we observe time-related defects, our medical device-specific packaging engineers have the expertise to offer solutions to get your product launch back on track.
That wraps it up for our 3rd pillar of packaging, Store! As a refresher, the Make pillar explains the process at which we make the seal for your sterile barrier packaging and the Ship pillar explains what testing is required to simulate what packages might endure during the distribution cycle.
If you have questions about your medical device packaging validation, contact us for a discovery meeting today to meet with our team of medical device packaging engineers.
* Typical temperatures are 50°C, 55°C, 60°C.
** Typically 22°C or 23°C.
*** We test to a 2.0 Q10 factor. 2.0 is a common and conservative means of calculating an aging factor (as mentioned in ASTM F1980 Section 7.3.1).