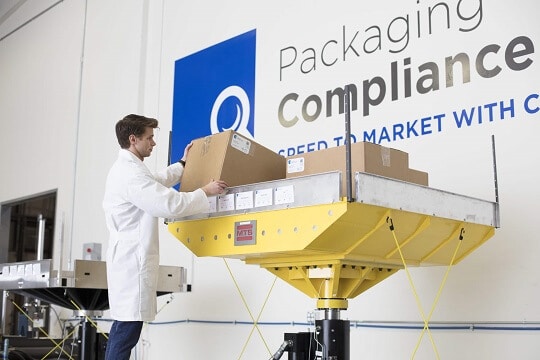
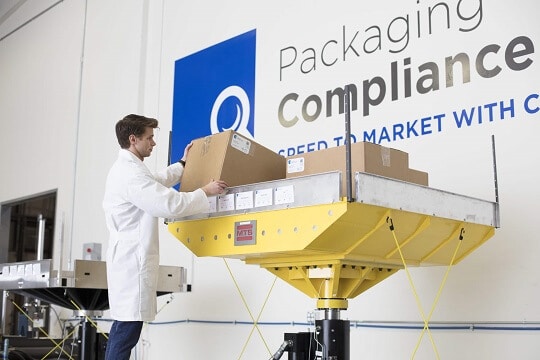
Why do failures happen more frequently during transit testing? The nature of transit testing is to simulate what the packaging will endure during the distribution cycle including drops at various angles & heights, stacking ability, altitude pressure changes, and high frequency vibrations. Therefore, when we are testing your samples, we give them a beating.
To help you understand what is happening inside of your box, think about someone driving their car. If the driver is not wearing a seat belt and they get in an accident, they are likely to be ejected from the car on impact, which we all know is not what we want to happen. On the other hand, if the driver is wearing a seat belt, their movement is mitigated by the seat belt and they stay in place.
This is essentially what we want for your sterile barrier and device, a packaging system that will keep the sterile barrier and device intact no matter how much it is thrown around. Your samples are precious cargo that need to be contained. We will consider what they will endure and create a plan that will get your products delivered unscathed.
Diving into Common Packaging Design Failures
Package Sizing
When you are determining the size of the pouch for your medical device, it is best to lay the pouch flat within the shelf carton to avoid folding the pouch if possible. A shelf carton is the small box that the sterile barrier and device fit into. Multiple cartons are often placed into a corrugated box and shipped to the end user. Devices are often left in the carton when removed from the corrugated box because they stack nicely on shelves within the inventory rooms of hospitals.
A common packaging design failure occurs when pouches do not lay flat and must be folded to fit inside the carton. When this happens “points” in the film can form. These points then rub up against the carton, or shipper, causing the film to abrade. Points can also be formed if you force a pouch into a carton that is too small or too many pouches in a carton or shipper.
Channel in Seal
Folding a pouch can cause creases (or channels) in the seal. These can be observed visually and then confirmed after performing a Bubble Leak or Dye Leak test.
If you are going to fold your pouch, it is imperative to use a material that is not going to develop a crease. This does not necessarily mean you should choose the thickest material. You want to look for a material that is thick yet flexible.
Containment Within Packaging
Internal abrasions are caused when the device rubs against the film from the inside because it is not contained properly. A root cause analysis will help our engineers determine where the abrasion is occurring and discover if part of the device is sharp or has a texture that is not contained which would lead to the internal abrasion. To resolve this, we would suggest adding a protection over the sharp components of the device. You could also add a backer card that the device straps to in order to immobilize the device within the sterile barrier.
Overpacking
A good rule of thumb when it comes to packing your samples is if you can shake the shipper and hear movement inside you should add dunnage (bubble wrap, foam, Kraft paper, or any other kind of protective packaging) to fill out the shipper. This reduces the movement and dampens the vibrations that occur during transit which in turn reduces transit testing failures.
Keep head space in mind for shippers. You don’t want a lot of moving room.
Drops
a. Seal Flexing
All too often customers assume they are in the clear in terms of transit testing because their device is in a tray.
Rigid trays with heavy devices inside are extremely susceptible to transit failures if there is not another material to absorb the shock from drop testing. These failures are often caused by flexing of the tray upon impacts. If dropped on its corner, the seal can flex, crack or the Tyvek lid to pop open.
A solution for this type of failure is to cushion the tray and/or carton with either corrugate or foam. The additional materials will absorb most of the shock on impact instead of the sterile packaging.
b. Device Punctures
Another example of a common drop failure is when the device punctures the pouch. In puncture failures, you will not see any creasing of flexing. Under a microscope the puncture looks more like a stab. Thicker material will help make this packaging puncture resistant. It will also ensure the sharp components are covered. Ensure there is enough dunnage inside the shipper to mitigate movement.
Choosing a packaging material that is resistant to puncturing is made easy with the ASTM F1306: Test Method for Slow Rate Penetration Resistance of Flexible Barrier Films and Laminates.
Even if your samples do experience transit related failures, there is usually a simple solution – we will investigate and determine what that solution is! The investigation phase is often referred to as a ‘Root Cause Analysis’. Figuring out the root cause will get your project back on track so your product will make it to market.
Packaging is our area of expertise and we can help you navigate some of these common problems in the packaging industry. If this information helps a medical device manufacturer make better decisions on their packaging before they send their samples out for testing, then we’ve done our job! Regardless, we are here to help you on this ride and are excited to help YOU avoid these common packaging design failures and speed your device to market!