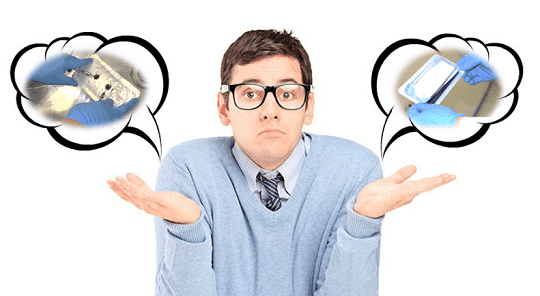
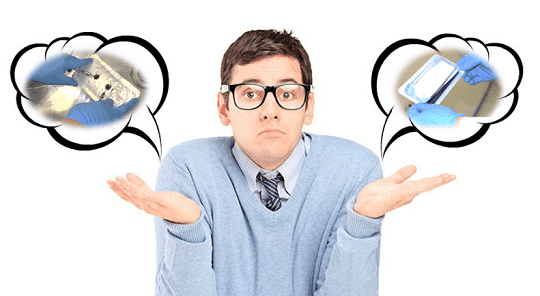
What Package Integrity Testing Do You Need?
Where your post-aging or -transit packaging validation efforts are best focused depends on several factors: what results did shelf life and distribution tests produce? How were your packaging materials selected? What packaging integrity testing has been conducted? The point is clear: you now know (or are in the process of learning) how your packaging behaved going forward in a truck and in time. What you may not know with certainty is whether sterility can be trusted to remain in tact after these experiences. Specifically, what aspects of the system should you subject to further testing?
What Can Integrity Testing Accomplish?
The key to integrity testing is to understand completely the relationship between your packaging and the physical characteristics of the medical device it contains. If you are validating the packaging system and its ability to make it through the distribution cycle while maintaining sterility, then ASTM F2096 Bubble Leak test is the way to go. This test uses internal pressurization while submerged in water to analyze the packaging system. Following specific protocols ensures consistent, accurate reporting of how the packaging performed. The test reliably reveals failures invisible to the eye, such as pin holes, cracks or micro-tears, that are associated with the packaging as a whole.
If you are validating a piece of equipment (probably a sealer) or assessing the quality of the seal that your equipment produces, schedule the ASTM F1929 Dye Leak test. To verify only seal integrity (i.e., if a vendor manufactured your packaging) ask about ASTM F1886 Visual Inspection testing. If you have in-house sealer equipment, it is important to have it validated, as well as the protocols you use. Without this, your cost-saving efforts can backfire. You may benefit from a Sealer Validation MicroProgram.
Is Integrity Testing a Must?
The bottom line is that testing and validating are not only facts of life, but are straightforward and efficient tasks when treated as part of the plan for your medical device from the beginning. Can you shortcut? Sure. Just as you can shortcut by putting the baby’s car seat in the car without buckling in the baby or maybe just skip anchoring the car seat to the car itself. The baby is the medical device, the car seat is the package and the car is the case packaging (and transit environment!). What could possibly go wrong?
Want to learn more about testing the integrity of packaging? Contact our team to learn about this or any of our test methods.