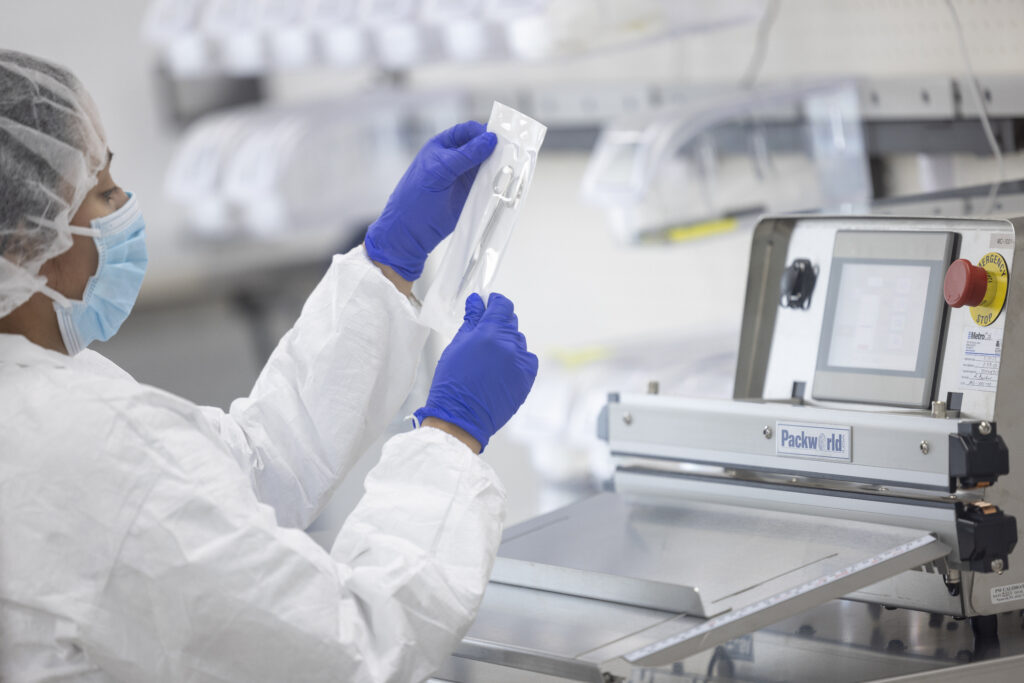
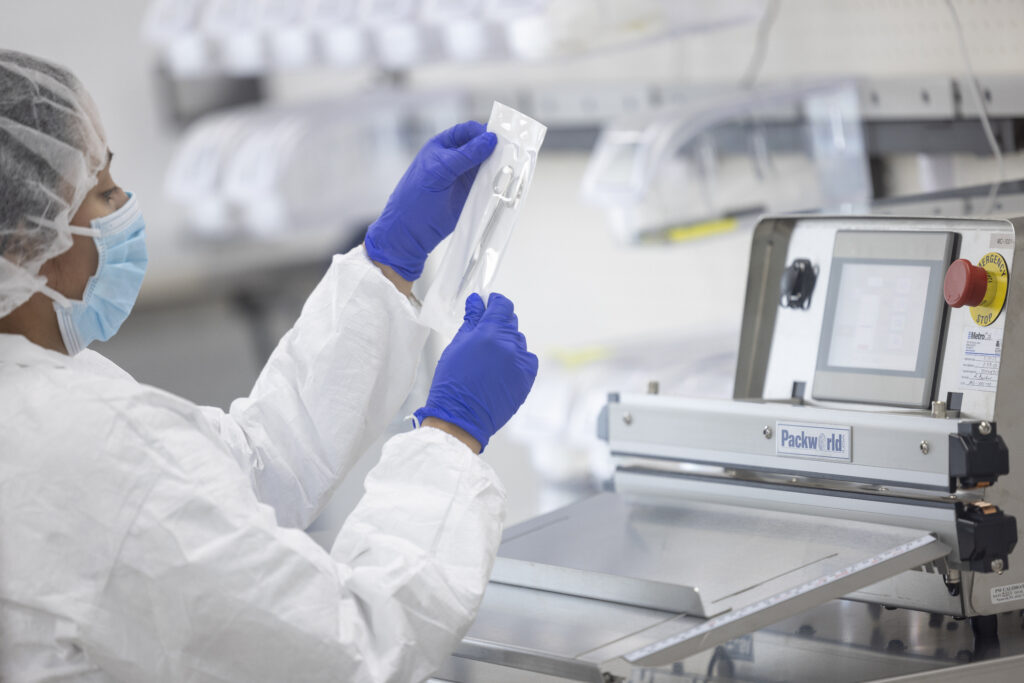
You might be wondering: Is statistical analysis really necessary in packaging, or can quality control be managed without it? The answer is clear—statistical analysis is not just beneficial, it’s essential. It drives efficiency, ensures compliance, and maintains product quality. Here’s how:
1. Quality Control and Assurance
-
- Defect Detection
Statistical analysis enables the identification of defects in packaging, such as improper seals, material inconsistencies, and defects in the form of leaks, pinholes and tears. By collecting data on defect types and frequencies, manufacturers can monitor trends and address issues proactively, ensuring that defective units are minimized in production.
-
- Process Optimization
Packaging processes involve multiple variables (e.g., time, temperature, pressure) that must remain within specific limits for optimal performance. Statistical tools like control charts are used to monitor these variables and ensure that packaging operations remain within defined specifications, reducing variability and improving consistency.
2. Sampling and Testing in Packaging
In many cases, it’s not feasible to inspect every package. Statistical sampling allows manufacturers to determine the number of samples required to make reliable quality assessments.
-
- Sample Size Determination
Full inspection of every unit is impractical, so statistical sampling methods (e.g., ANSI/ASQ Z1.4) are used to calculate the minimum number of samples required for testing. These methods balance the need for reliability with efficiency, ensuring that quality standards are met with minimal testing
-
- Acceptance Sampling
Acceptance sampling involves selecting random samples from a batch to assess whether the entire lot meets quality specifications. By applying statistical techniques, manufacturers can make decisions about batch acceptance or rejection based on the sample data, reducing the need for 100% inspection while ensuring quality standards are met.
-
- Package Integrity Testing
Tests like dye testing (ASTM F1929) and bubble leak testing (ASTM F2096) rely on statistical analysis to assess the integrity of packaging. These tests are conducted after simulating real-world conditions to verify that the packaging can withstand transportation, handling, and storage conditions. Statistical methods are used to analyze the results and determine if the package meets the required performance standards.
3. Regulatory Compliance and Statistical Analysis
For industries such as medical devices, regulatory compliance is essential. Statistical analysis supports manufacturers in meeting the stringent packaging standards set by regulatory bodies like the FDA, ISO, and ASTM.
-
- Validation and Testing
Statistical techniques are essential for validating that packaging materials and processes comply with regulatory standards (e.g., FDA, ISO, ASTM). This helps ensure that packaging is safe, functional, and effective, meeting the necessary standards for consumer safety.
-
- Sampling Plans for Compliance
Regulatory agencies often mandate specific sampling procedures to demonstrate compliance with packaging standards. Statistical analysis helps manufacturers determine how many units need to be tested to ensure the batch meets the required standards, ensuring that sampling is both efficient and compliant.
4. Risk Management with Statistical Tools
Statistical tools also play a crucial role in identifying and mitigating risks associated with packaging failures.
-
- Failure Probability Analysis
Packaging must protect products throughout the supply chain. Failure Mode and Effects Analysis (FMEA) and reliability analysis are statistical tools used to assess the likelihood of packaging failures under different conditions. These analyses help manufacturers anticipate potential failures and design packaging solutions that minimize the risk of product damage.
-
- Data-Driven Decision Making
Statistical methods like hypothesis testing and confidence intervals are used to inform decision-making. These tools enable manufacturers to determine whether a batch should be accepted or rejected based on data, reducing the reliance on subjective judgment and improving consistency.
5. Cost Efficiency Through Statistical Analysis
Statistical analysis also contributes to cost efficiency by reducing waste and optimizing testing processes.
-
- Reducing Over-Packaging
By analyzing the packaging process, statistical tools identify inefficiencies such as excessive material use or high defect rates. Optimizing these areas helps reduce waste, lower costs, and improve the overall packaging process.
-
- Optimizing Sample Sizes
Statistical analysis ensures that the smallest number of samples required for reliable testing is selected. This reduces unnecessary testing and resource use, improving operational efficiency and lowering costs.
Common Questions
Q: How should one determine the sample size for packaging tests?
A: Both regulatory guidelines and statistical analysis methods can guide sample size determination. Industry standards provide a baseline, but tools like FMEA help assess risk levels and tailor the sample size to ensure that testing is adequate without over-testing.
Conclusion
Statistical analysis is an essential component of the packaging process. It ensures product quality, facilitates regulatory compliance, manages risk, and improves cost-efficiency. By applying these methods across the packaging lifecycle, manufacturers can enhance operational efficiency and deliver reliable, high-quality products to the market. Statistical analysis isn’t just beneficial—it’s a fundamental requirement for modern packaging operations.
Would you like more information on statistical analysis? Reach out to PCL to be connected with one of our expert packaging team members today!