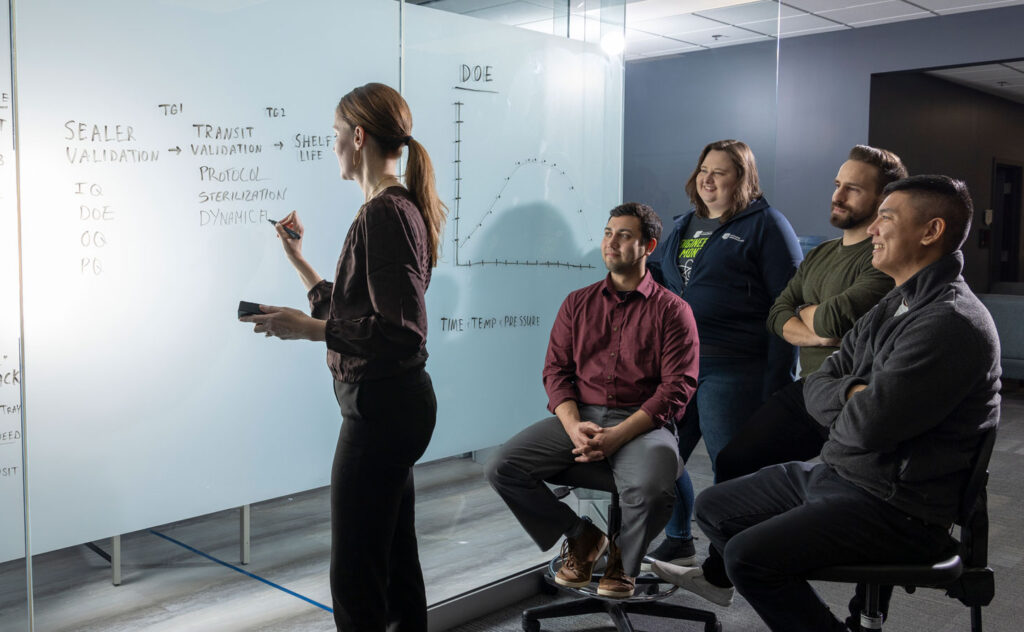
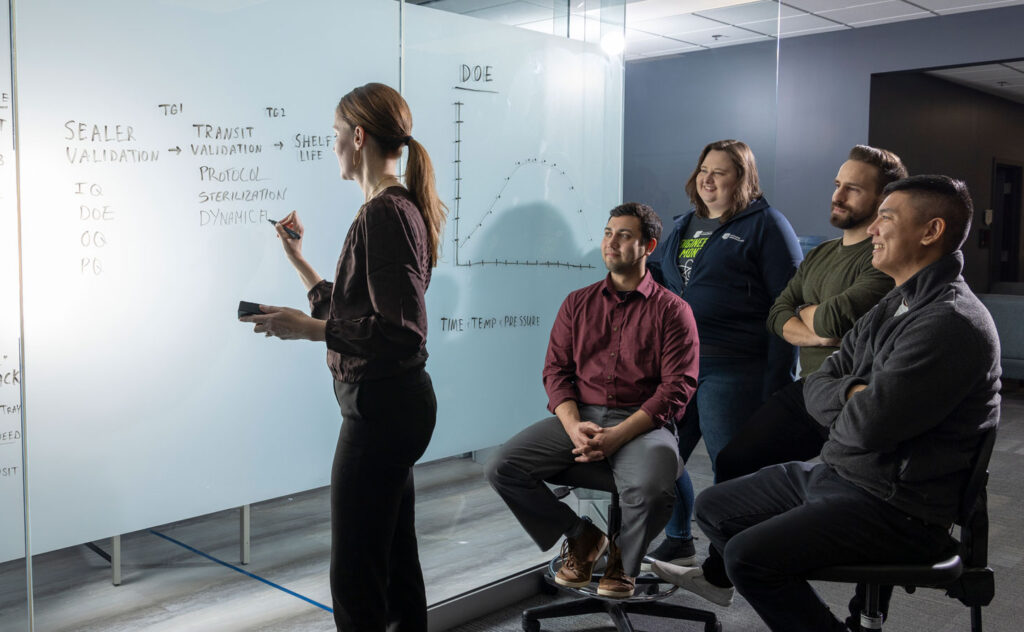
Twice a year, the ASTM D10 and F02 Committees come together to ensure that industry packaging standards remain accurate, relevant, and up to date. These committees are essential for anyone in packaging—especially in fields like medical devices, where regulatory compliance and performance standards are critical. Let’s dive into how these meetings unfold and what it means for the sterile packaging industry.
A Virtual Twist and an International Touch
This fall, while the D10 Committee, originally slated to meet in Orlando, Florida, had to move its meeting online due to a hurricane, the F02 Committee’s meeting proceeded as planned. F02 members hopped on flights to Bologna, Italy, to collaborate face-to-face—a valuable aspect of these meetings where nuanced, in-depth discussions are necessary. These meetings go beyond mere updates; they represent a chance to collaborate closely with industry experts on the finer points of standards development.
ASTM D10 and F02 Committees: A Breakdown
The D10 Committee focuses on outer packaging standards. Its discussions center on the performance of transit containers and secondary and tertiary packaging—key elements in ensuring products survive the distribution environment. Standards like ASTM D4169 and ASTM D4332 fall under D10’s purview. The committee’s work is segmented further into subcommittees, allowing specialized focus. Together, these subcommittees review ballots on standards up for reapproval, revision, or withdrawal ensuring they still hold up to industry needs and technological advancements.
The F02 Committee, on the other hand, deals with primary barrier packaging—think of the seals and materials that directly contain and protect a product. This committee oversees standards such as ASTM F2096 (for bubble leak emission) and ASTM F88 (for seal strength testing). Like D10, F02 also operates with various subcommittees to manage specific areas of expertise and interest.
The Process Behind Revising and Developing Standards
During these gatherings, committee members review old standards and discuss any new ones under consideration. New technologies, updated equipment, or innovative processes often prompt standard revisions. When this happens, committee members work together to adapt the test methods, ensuring new procedures align with the latest industry developments. Because each standard must be reviewed every five years, there is a constant need to refine, update, or occasionally withdraw a standard based on its relevance and performance in today’s market.
To develop or revise a standard, these committees follow a rigorous process. First, subcommittees address specific ballots and resolve any open issues. Since ASTM standards require 100% consensus to pass, achieving agreement can be a lengthy process. The committees use data from inter-lab studies to ensure that standards are driven by evidence rather than individual business interests.
Getting Involved in ASTM
One of ASTM’s strengths is the diversity of voices involved in shaping these standards. Participation is open to various stakeholders: suppliers, packaging manufacturers, equipment makers, medical device manufacturers, and end-users. By bringing together such a wide range of perspectives, ASTM maintains a balanced approach without the influence of government lobbying, ensuring the standards remain relevant, neutral, and beneficial across the industry.
Why These Biannual Meetings Matter
The biannual D10 and F02 Committee meetings are crucial in keeping packaging standards aligned with the latest industry advancements. Face-to-face interactions—whether in person or virtual—facilitate complex discussions, enabling the committee to tackle technical challenges, address disagreements, and ultimately push for 100% consensus on ballots.
For PCL and other companies that rely on ASTM standards, staying involved in these committees helps ensure they’re not only compliant but also actively contributing to the evolution of industry practices. Whether you’re a packaging supplier, medical device manufacturer, or equipment provider, ASTM’s work provides a foundation of trust and reliability that underpins product safety and efficacy across the packaging sector.