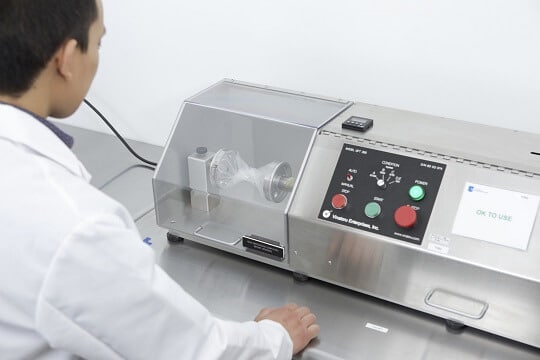
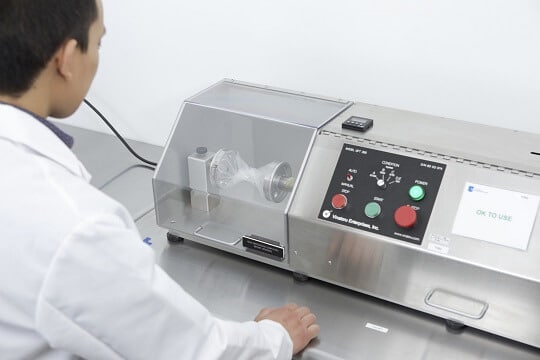
Most of the packaging we validate is required by the FDA to undergo ISO 11607 validation tests to make sure the packaging remains sterile during the distribution cycle. However, there are instances that require us to dive in a little deeper and perform tests that are outside our regular scope, and not ISO 11607 requirements, for the benefit of the client. One of those tests we will be discussing in this blog is a Gelbo Flex Test.
What is Gelbo Flex Testing?
Gelbo flex testing is a standard per ASTM (ASTM F392: Standard Practice for Conditioning Flexible Barrier Materials for Flex Durability). As mentioned above, gelbo flex testing is not a required method for bringing a medical device to market. Rather, it is used as an R+D (research and development) tool to evaluate the relative ability of one of more materials to withstand repeated flexing.
The goal of this test method is not necessarily to have zero cracks or tears, but more to evaluate the performance of one material versus another and an expectation for there to be cracks to assess. If there are no cracks, the cycle count is likely too low, or the material is a specialized material that refuses to crack. It simulates what the packaging material might endure during transit testing, specifically during the vibration portion.
Medical device packaging material manufacturers perform the gelbo flex test on their packaging materials so medical device manufacturers have and idea at how much stress a specific packaging material can endure during transit testing. They will typically have that spec listed on their material sell sheet. This specification is important to know so you know the materials ability to flex, fold, compress, or compound without cracking.
How a Gelbo Flex Test is Performed
Material that is a nonporous, flexible film can be used for gelbo flex testing. Typically, this is a clear plastic film that you would see on the on the reverse side of Tyvek pouch or foil material for a foil-to-foil pouch.
The first step is to cut a swatch of film that is about the size of 1 piece of printer paper. Then, the swatch is mounted on the gelbo flex tester by curling the swatch around the two round mandrels.
When we start the gelbo flex tester, one of those mandrels will twist and compress together and then open back up and untwist. This is done repeatedly to simulate the flexing that materials endure during transit testing.
After the film swatch has been stressed, we fix it to a white paper backing. Once the swatch is secured, we essentially paint it with the blue dye we use for seal integrity testing by dye leak ASTM F1929. If there are any pinholes or flex cracks, the toluidine blue dye will leak through and stain the white paper backing. From there we can observe the crack patterns.
Some variables we might control are number of cycles we expose the materials to. This could range from 250 – 1000 cycles.
Why PCL Would Use Gelbo Flex Test
Since gelbo flex test is not required validation method to bring a medical device to the market, why would PCL perform this test? The simple answer is that we want to be resource for our customers and help them anyway we can. A few examples of this are:
- Client A has been using X packaging material for the duration of our business relationship and has not had any issues. If that packaging material becomes discontinued or has changed in some way, the client will need to find a new material for their device. In this case, we would offer to run gelbo flex tests on their potential options and provide them with our findings along with which material we would recommend based on the test results.