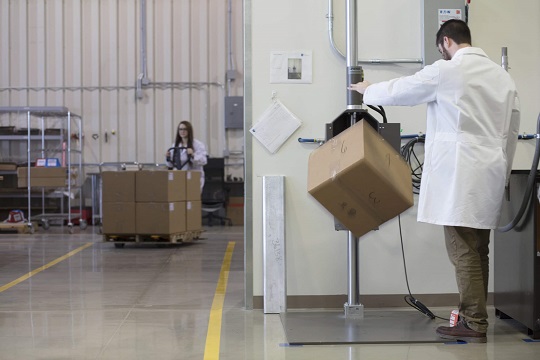
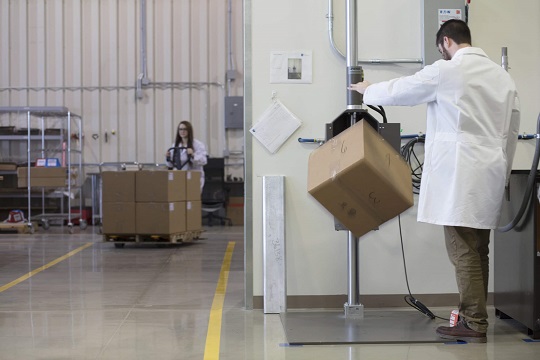
The first blog post in our series about the packaging validation process and guidelines was about the process that is required to create a good seal for sterile barrier packaging. We call this step the ‘Make Pillar’ at PCL. Now, what is next?
Because we follow ISO 11607, the next step in the sterile packaging validation process is distribution transit testing. At PCL, we call this step the ‘Ship Pillar’.
The ‘Ship’ Pillar
The ‘Ship’ pillar commonly has three phases of testing: Environmental Conditioning, Transit Testing, and Integrity Testing. Environmental conditioning and transit testing are performed to make sure a package can withstand the rigors and environment of the distribution cycle. We close out the ‘Ship Pillar’ with Integrity Testing to ensure that the sterile barrier is still intact after we shake, rattle, and roll your samples!
-
Environmental Conditioning
The primary standard our clients request for environmental conditioning is ASTM D4332. Environmental conditioning simulates the varying climates that packaging might endure in the back of a shipping truck. If our customers know the routes their packages will travel and can provide that data to us, we can test to those profiles. It is more likely that customers will not have this information, so we run three standard climatic profiles to cover the worst-case scenarios. Those profiles are:
- Tropical (High temp, high humidity)
- Desert (High temp, low humidity)
- Subzero (Low temp, low humidity)
Environmental conditioning is necessary because the varying temperatures and humidity can affect a seal’s integrity. For example, high temp and/or humidity could soften cured adhesives, causing a weak seal to peel apart and cold temperatures could make a package brittle.
There are several other standards that can be used for environmental conditioning such ASTM F1825 or ISTA 3A. PCL can help you select the correct standard and conditions for your next transit text.
-
Transit Testing
Transit Testing Standards for Medical Device Packaging
The two standards that the FDA recognizes for medical device packaging are ASTM D4169 and ISTA 3A, so those are the two we always recommend. Based on the package type and distribution method, there are different standards we can use for testing.
We offer ISTA 1A and 2A as well, but we wouldn’t recommend using either of those standards for your sterile device packaging unless you have data to prove you don’t need your samples to be tested under ISTA 3A or D4169.
ASTM D4169
ASTM D4169 is a set of test methods that will accurately challenge your package system if you do not know the exact path your device will be shipped in a small parcel environment.
ASTM D4169 has 18 distribution cycles within it. We select the one that is most appropriate based on what you think your packaging will endure during the distribution cycle in the real world. The most common distribution cycle is DC13, which is a truck and air profile. Within DC13 there are 7 tests. Those are:
Schedule A: Handling (Drop testing)
Schedule C: Stacking (Compression testing)
Schedule F: Loose-Load Vibration (Vibration testing)
Schedule I: Low Pressure (Aircraft Simulation)
Schedule E: Vehicle Vibration (Vibration testing)
Schedule J: Concentrated Impact (Dart)
Schedule A: Handling (Drop testing)
As you can see, transit testing begins and ends with drop testing with a lot of vibration testing in the middle. This is to simulate what a distribution path is like in the real world. The drops at the beginning simulate sorting at the distribution facility. Vibrations and compressions represent the package traveling in the back of a shipping truck and having packages stacked on top of it. The drop at the end simulates the final drop off, wherever that might be!
Just like there are multiple distribution cycles, there are three assurance levels. Assurance level 1 is the most extreme and 3 being the least extreme. Medical device companies almost always run assurance level 1, with a few exceptions if they have the technology to track the distribution cycle of their samples. If we are making a recommendation to a medical device company with a sterile device, we will always recommend AL1.
ISTA 3A
ISTA 3A is an alternative test to ASTM D4169. The difference is that ISTA provides schedules that cater to shipping units that vary in size. Depending on the shape and size of the packaged products depends on the kinds of tests that are required.
-
Integrity Testing
When we do package integrity testing post-transit the focus is on the whole packaging system. Therefore, the tests we perform in this phase are slightly different than the integrity tests we perform when we are in IQ/OQ/PQ (ie: dye leak testing).
Bubble Leak Test is a great test for testing the whole package because we are submerging the entire package underwater. Once the package is submerged and we have increased the internal pressure what we are looking for here is a steady stream of bubbles. If we see a steady stream, it is an indicator that there is possibly a breach in the package.
We can also evaluate the label or barcode to make sure that the label has not rubbed off and is still easy to read or has not scuffed off any ink. A failure for the label is if two or more characters are rubbed off.
Like we mentioned at the top of the article, 1 out of 3 transit studies fail. One cool of the many cool things about PCL is that we are not just a package testing lab, we also have medical device specific packaging engineers in house. Because our engineers are so knowledgeable about the testing that happens, we’re able to create package designs to negate potential failures. With that said, failures do still happen, but having that knowledge helps us to figure out how to fix it faster. We can also perform Root Cause Analysis studies to help our clients determine the cause of any transit-related failures observed in the lab.