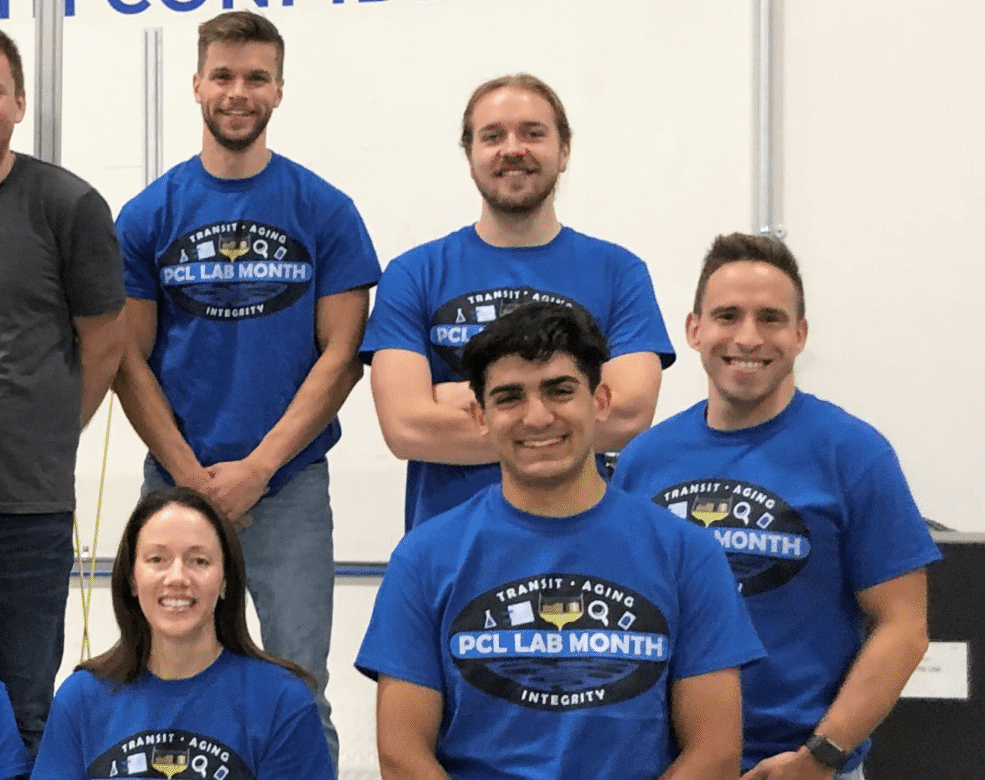
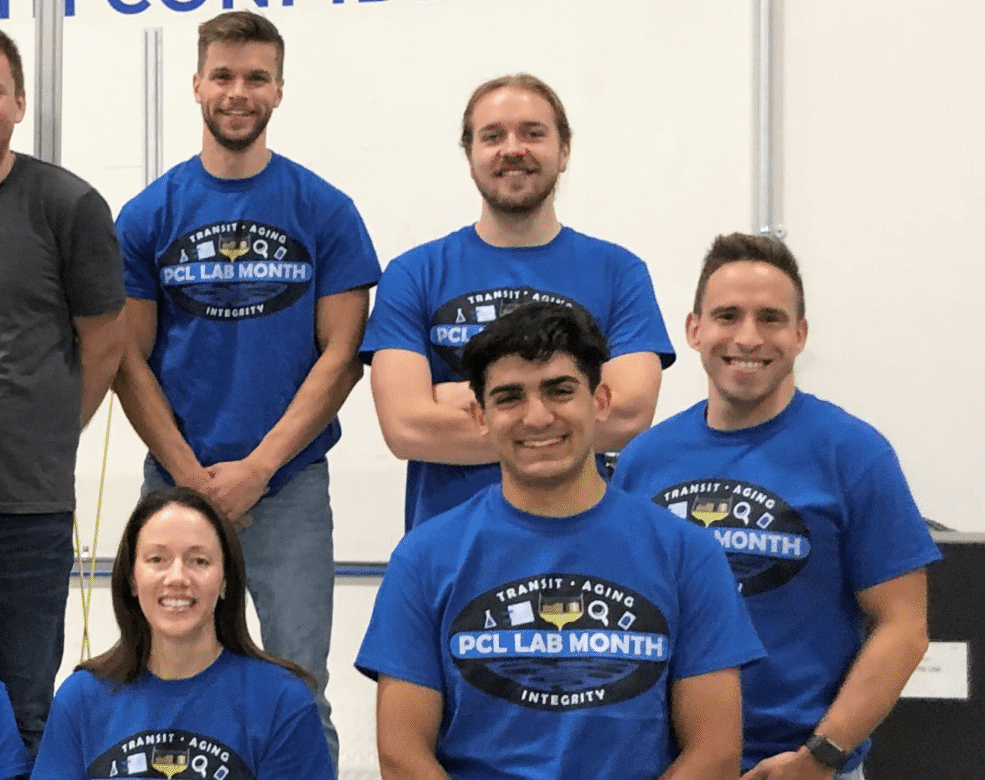
We’re sad to be sending off one of our packaging engineering interns this week, Jacob Barash. Before interning at PCL, Jacob wasn’t fully aware of the medical device packaging industry and was using this as an opportunity to learn. And boy did he learn!
We pride ourselves in providing our packaging engineering interns with an experience that will benefit them in their professional life by working on actual client projects (aka no coffee runs for the rest of the office). During his internship, Jacob learned how to perform many of the packaging integrity tests we see in our lab every day, he was involved in validating new equipment used for package testing. Jacob also had the opportunity to work on multiple packaging projects for a client who is known globally.
We wish Jacob the best and will reluctantly send him off to finish up his final semester at Michigan State University where he is majoring in Packaging. To learn more about Jacob and his experience as an intern at PCL, continue reading!
- Cassie Peterson, Marketing Manager
CP: What inspired you to pursue medical device packaging?
JB: Going into college, I wasn’t exactly sure what I wanted to major in, but I knew I wanted to be an engineer. I started out college majoring in Mechanical Engineering at Michigan State University but quickly realized it was not the path that I wanted to pursue. After some research and a conversation with my dentist, I learned about an unusual engineering-based career path called ‘packaging’. My dentist told me “It’s a major where you could make as much as other engineers without having to take calculus 4”. As an eighteen-year-old that sounded very attractive. I decided to take Packaging 101 at MSU to see what packaging was all about. That class taught me that packaging was much more than the name justifies it as.
After taking the intro packaging class I knew this was a career path I wanted to pursue. The next step was deciding what industry I wanted to go into. I figured I would search for an internship opportunity first and use real-life experience to see if I enjoyed the industry or not.
One of my main objectives when searching for an internship was to find an opportunity where I felt I could learn as much as possible. After some searching and a few more packaging classes, I heard about a company called Packaging Compliance Labs looking for a packaging engineering intern. I did not know much about medical device packaging at the time, but I wanted to learn so I applied for the position. Little did I know this would be a life-altering decision.
During my amazing experience at PCL (we didn’t pay him to say that!), I learned medical packaging is the industry I want to have a future in. Medical device packaging has a lot of regulations and laws surrounding it. This creates a challenging yet exciting environment where you not only have to protect and ensure the sterility of the product but also need to have knowledge on what regulations must be followed. I believe medical device packaging engineering is a fulfilling profession because of how important the packaging is for a medical device. Being able to have a hand in the process of launching new lifesaving medical devices to market is something I look forward to every day.
CP: Why do you think packaging is important?
JB: A perfect way to exemplify the importance of packaging is to use the example of COVID swabs and how hospitals and testing facilities were able to have those delivered with the sterile barrier still intact.
First, how do you transport the swabs from the manufacturer to the sterilizer? A package must be made to hold the swabs and protect them from the harsh conditions that might occur during transit. Events like a heavy shipper falling on top of our shipper full of COVID swabs, stacking too many shippers on top of our COVID swabs, or even something as simple as the vibrations from the truck driving on the expressway can breakdown the packaging and then deform the swabs. Therefore, the outside shipper not only holds the swabs but also protects them.
Once the swabs arrive at the sterilizer and undergo sterilization, how do we keep the swabs sterile and the packaging intact? A smaller package must be made to maintain the sterility of the swab. Once the sterile swabs get to the hospital how do the nurses know how to open them or how long their shelf life is? The manufacturer of the swabs must note those items of information on the package and label. As you can see a lot more goes into a medical device package than you would expect, and many different processes must be considered when creating a sterile barrier packaging system.
Medical device packaging is a unique profession where you must be very technical and be able to logically think through the steps the product will go through to create the best package system possible. At the same time, you cannot take the same approach for every package because every product is different therefore each product will have different packaging needs. This creates the need for compromise and thinking outside of the box.
CP: What was your favorite project you worked on while interning at PCL?
JB: While working at PCL I had the opportunity to take part in many different projects that I really enjoyed so I will give an overview of a couple of my favorites.
Early on in my internship, I got tasked with setting up the recently acquired label printers. These labels are a key part of the packaging as they convey important information and per GS1, ISO-15415, and ISO-15416 standards they are required on medical device packaging. The initial setup of the printers provided me the opportunity to learn the software that is used to create labels. Not only did I get to learn the software, but I also got to learn about the regulations that are the foundation of medical device package labels and apply some of that knowledge in an Operational Qualification.
Another one of my favorite projects was a large project where I got the opportunity to take part in all steps of the sealing and validation process of an updated medical device package. This project solidified the whole process of packaging validation since I got to take part in almost every step. Since this was such a large and complex project, it also taught me the importance of clear communication with others and staying organized in each step of the packaging validation process.