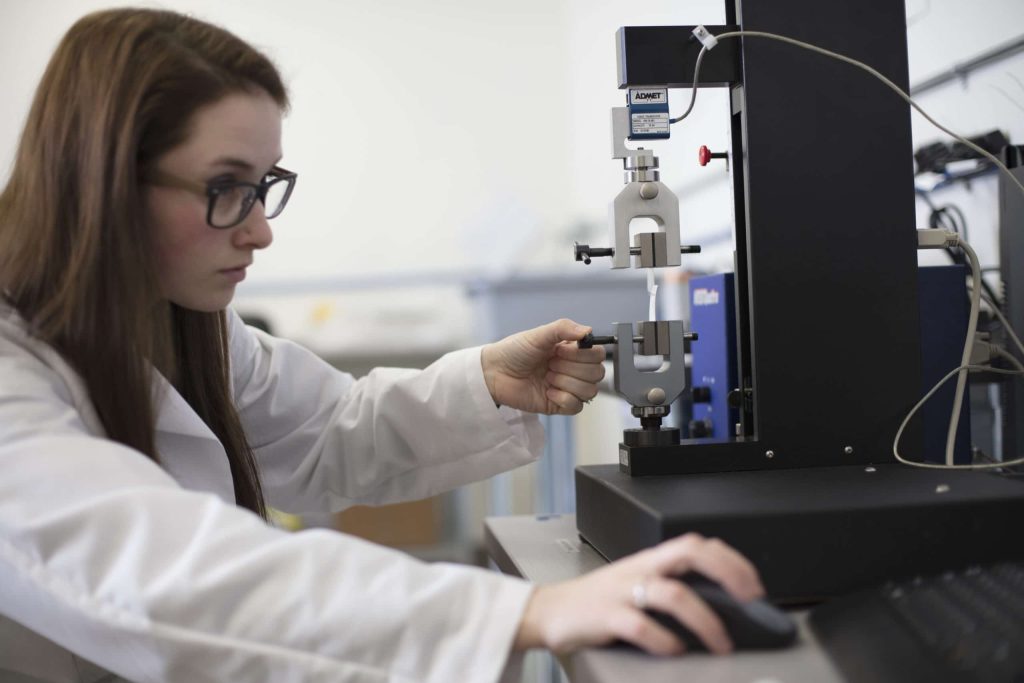
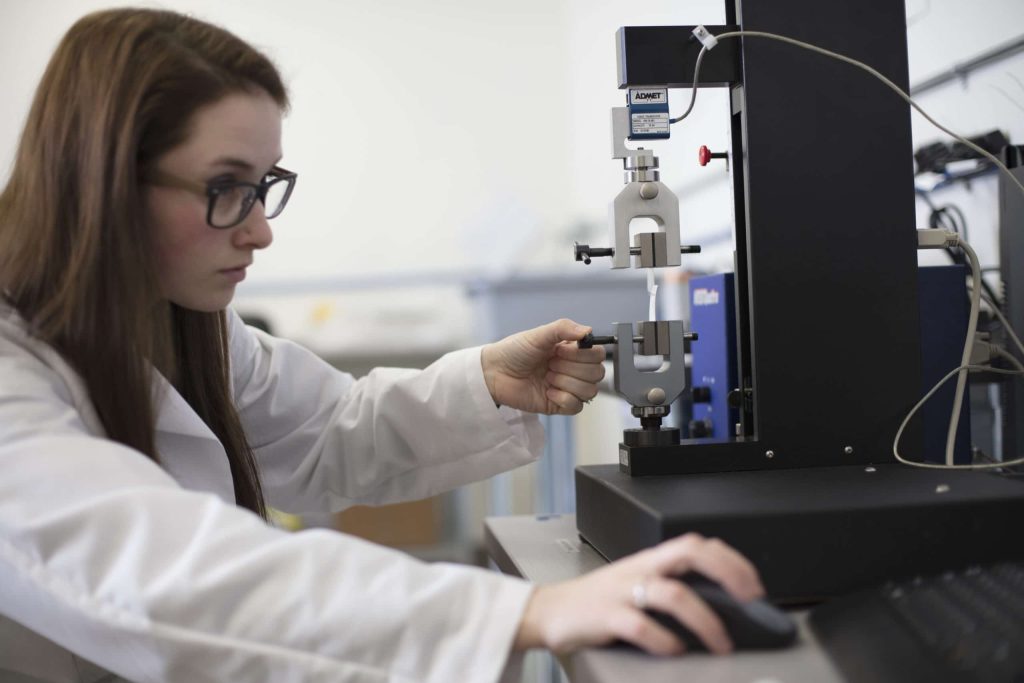
ASTM F88 is a standard that explains how to perform a test method for seal strength. This test method alone does not tell us much besides the force it takes to separate the materials. In this blog, we will explain how other processes, like a Design of Experiments, help us determine the optimal seal strength for sterile barrier packaging.
When we are testing for seal strength, what are we measuring and how is it measured?
Seal strength per F88 measures the force required to separate a test strip of material containing a seal. The units in how seal strength is measured can vary. Specimen width is the first factor that needs to be considered. The three approved width measurements we use for this test method are 1 inch, .984 inch, or 15 ml.
The next consideration is speed. The speed, or rate of separation, can be between 8 to 12 inches per minute. This factor tells us the speed at which the jaws of the test equipment are coming apart from each other.
Lastly, which units will we use to measure seal strength? Our two options for units are pounds and Newton’s. We typically report this in Newton’s per 15 mm or pounds per inch.
How do you determine if a seal is too strong?
When the seal is too strong you typically begin to see mottling occur in the material. Mottling is when the material melts or curls. Mottling is the beginning stage of the material becoming translucent, or opaque. If a seal has mottling, is translucent, or is transparent, the seal will receive a bad visual score. (We will learn a little later in the blog that visual scoring is one of the factors that determines what a good seal is!)
If a seal is too weak you likely would not see seal transfer which would also result in a poor visual score.
What is good seal strength from a sealing process standpoint?
Seal strength needs to be thought of in a multifaceted way. The process of determining what makes a good seal is the ‘Make’ pillar in ISO 11607. For the ‘Ship’ and ‘Store’ pillars you must think of what good enough seal strength is to maintain the integrity of the sterile barrier. Those are the two examples of factors that play into what good seal strength should be.
This is defined by conducting a design of experiments (DOE) or sealing process characterization exercise.
What happens during a Design of Experiment (DOE)?
ASTM F88 is a test method in which packaging engineers can define seal strength requirements, like a minimum seal strength.
We define what minimum seal strength is by conducting a DOE to find out what is the best recipe for seal strength and visual score. Conducting a DOE allows us to figure out which factor has a greater effect on seal strength and visual quality.
The factors that define recipes are temperature, time, and pressure. We will create samples for each recipe and then visually grade the seal quality of that recipe and record that data. Next, we conduct seal strength testing and record data. The last step is to convert all the data we gathered and put it into a plotted graph. The plotted graph allows us to identify what we can consider good seal strength.
Below is an example of what a DOE plotted graph could look like. On the X-axis we have temperature. On the Left Y-axis, we have Seal Strength and on the Right Y-axis, we have Visual Score. The solid line represents average seal strength and the dotted line represents the average visual score.
When determining which recipe we should use we’re looking for the perfect window where the seal strength is adequate and the visual score is high.
If you look at the graph, we are looking for the trend of factors that creates an appropriate amount of energy transfer that yields acceptable seal strength and visual score. In our experience, pressure is the least impactful factor but needs to be considered as important during our DOE when validating a sealing process. That being said, time and temperature are typically the more impactful factors. How much energy (temperature) is being exerted onto the packaging materials? How long (time) should the sealing process be exerting said energy onto the packaging materials? These are the things our packaging engineers have to consider when determining what an acceptable ‘recipe’ is.
For example, if we look at the beginning of the yellow solid line at 103ºC, the seal strength values and visual score are both low. At 190ºC we see higher seal strength values, but because we observe slight mottling, the visual score trend becomes negative. Between 165ºC and 190ºC the seal strength and visual scores are both considered acceptable, so this range of time, temperature, and pressure may be considered our process window!
If you have ever wondered what a DOE is or was confused about seal strength, we hope this blog made those processes more clear and easier to comprehend!
Ready to get the ball rolling on your medical device packaging validation?
Contact us today!