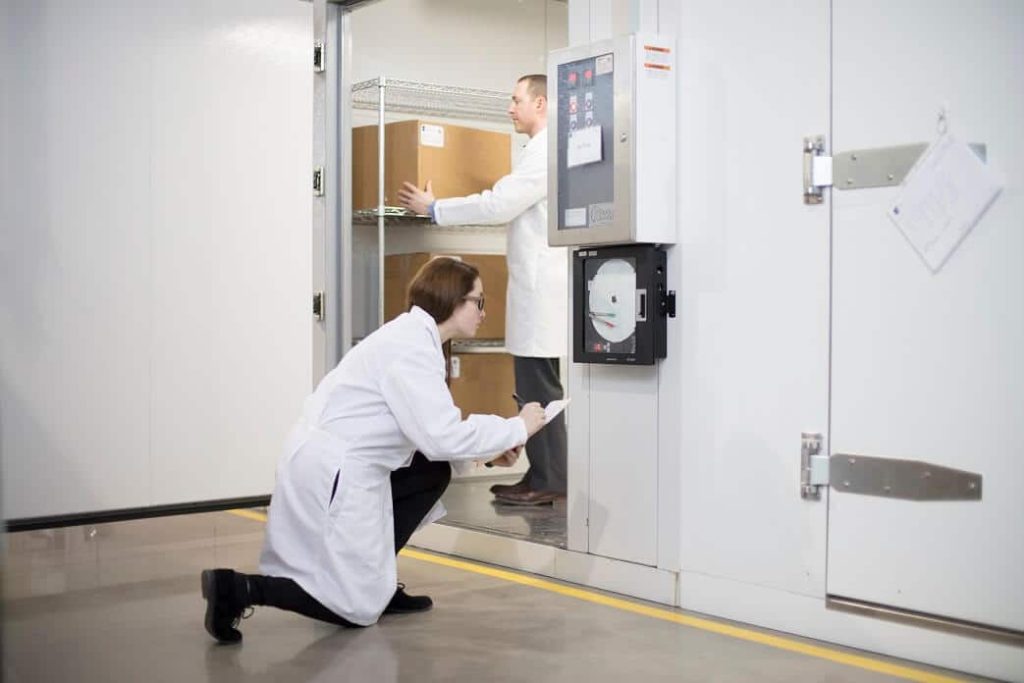
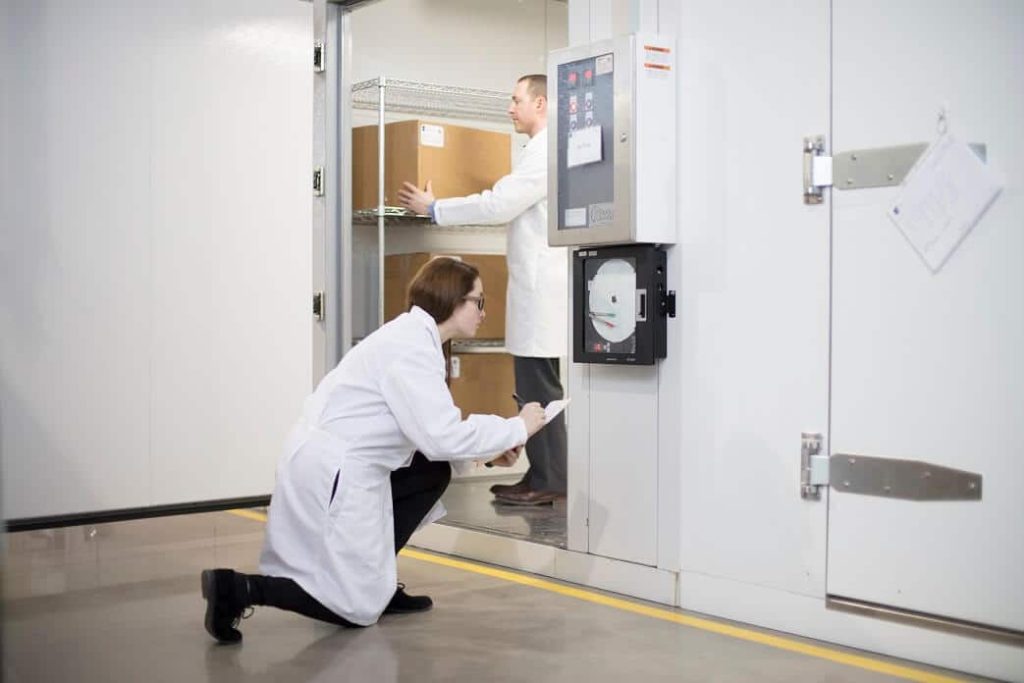
A potential customer calls us with a goal to have their product launched in the upcoming quarter with a shelf life target they must meet. If they are discovering sterile barrier packaging early on in product development, it is easy to plan around the packaging validation timeline. However, too many times we are brought into the picture at the end of product development. In these cases, the timeline for packaging validation is crunched. When this happens, it is our job to provide our customers with our medical device packaging validation expertise and find ways to make their timeline work, which often involves real time aging and accelerated aging testing and shelf life studies.
Per ANSI/AAMI/ISO11607-1:2019 Packaging for Terminally Sterilized Medical Devices, it is a requirement that sterile packaging can maintain a sterile barrier to the point of use or expiry date. Something to keep in mind, is that per the standard, real time aging is absolutely a requirement. However, you may elect to put the product into market based on the preliminary results of accelerated aging studies, so long as the results of real time studies substantiate these shelf life claims in the future. It is always a best practice, and something we see becoming more and more on auditors’ radars, is that accelerated and real time aging studies are most appropriately kicked off simultaneously.
For accelerated aging, the FDA consensus standard is ASTM F1980 Accelerated Aging of Sterile Barrier Systems for Medical Devices is the most appropriate standard for medical packaging.
The first part of testing (transit and materials) is wrapped up quickly while accelerated aging tests can take anywhere between 29 to 57 days to complete*. We know that time is money, and the quicker accelerated aging is complete, the faster you can go to market with your medical device.
A question we get asked often is how we can speed up the accelerated aging portion of a customer’s sterile barrier packaging validation. The problem with decreasing the amount of time an aging study takes to complete means increasing the temperature of the aging chamber. In doing this, we could cause defects that would never happen in the real-world setting (think a hospital storage room).
In this blog, we will go over how we choose the temperature for accelerated aging studies and why increasing the temperature might not be a great option.
How does the temperature you choose affect your Accelerated Aging study?
A high temperature aging test can affect your study in a couple different ways. The higher the temperature, the less time it takes to complete the accelerated aging study.
The standard for accelerated aging uses an equation called the ‘Arrhenius Equation’. The output of this equation tells us how long the samples should be in the chamber for. If the temperature of the chamber were 55C and we were testing for 1 year in real time, the Accelerated Aging study would take 40 days. If we bump up the temperature to 60C and were testing for 1 year in real time, the accelerated aging study would be complete after 29 days. (Note: this assumes a Q10 value of 2.0 (the most conservative and default election, as outlined in F1980) and a real-world storage temperature of 23’C (again, a conservative and common selection)).
Did you know we have an accelerated aging calculator on our website? Find it here!
Something to keep in mind is the higher the temperature for accelerated aging, the farther you get from the ambient temperatures the sterile barrier packaging will experience during Real Time aging. The less like the real-world medical device storage temperature and overall conditions are, the more likely you are to create an unrealistic defect in your packaging. We will talk more about this later in the blog, but a solution to this is to run two aging studies at the same time at different temperatures.
What’s Humidity Have to Do with It?
Traditionally humidity is not a factor that is given much consideration. Because some of our team of packaging engineers actively engages with members on ASTM committees, we are learning the standard will be updated in the future to accommodate this factor. Since ASTM 1980 does not call out what the humidity should be set to, it is best practice to keep the humidity low. Just like heightened temperature, high humidity can create defects that are not relative to the real-world environment the sterile barrier packaging will experience. Our goal is to target less than 20% Relative Humidity (RH) for accelerated aging studies.
Aging Related Defects
The defects that we look for in aging studies differ from the defects we look for in any other kind of study. During transit simulation we drop shippers and shake them around, therefore the defects we are looking for after transit simulation are event related. When the defect is caused by dynamic forces of drop & vibration is happening to the samples, we call those defects event related.
In aging studies we are looking for time related defects. Some examples of this are:
- over time seals can soften and loosen up
- there might be tension in a package
- the material can delaminate
- The packaging could change in color
What if I REALLY need to wrap up my aging study? What are my options?
The one thing we could do is run two accelerated aging studies in parallel. This would require double the number of samples, but it could potentially speed up the accelerated aging portion of your study.
We would run both studies at the same time and test the samples for the first study after 29 days. If we find there are defects associated with the temperature being too hot, we will continue with the longer study. If we tested them and there were not unrealistic defects, we could end the 40-day study and use the data from the 29-day long study!
Anxious about your product timeline? Don’t sweat it! PCL will help you speed your medical device to market! Learn more about our services and testing methods.
*29-57 days = 1 year. This increases as your RT shelf life increases.