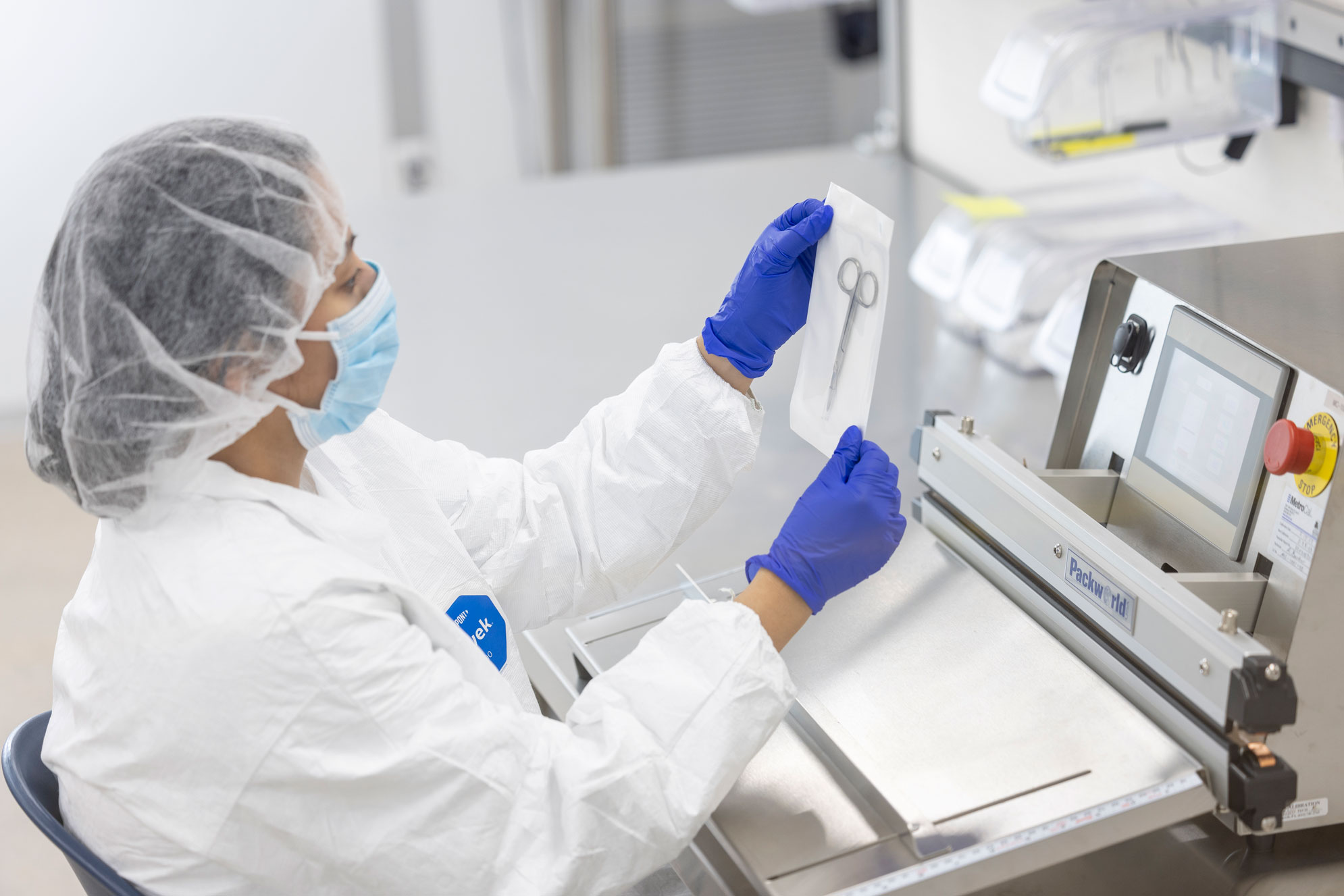
Sterilization Validation & Sterile Product Management
We help clients achieve sterilization validation and will manage that process for them. PCL partners with third-party sterilization providers to ensure the correct sterilizing agent and the characterized exposure required to achieve sterility. Methods include Gamma, EO, and E-Beam.
What is included in our Sterilization Validation and Sterile Product Management Service?
R&D Cycles
Sterilization Validation
Single Lot Release
Routine Processing
Quarterly Dose Audits
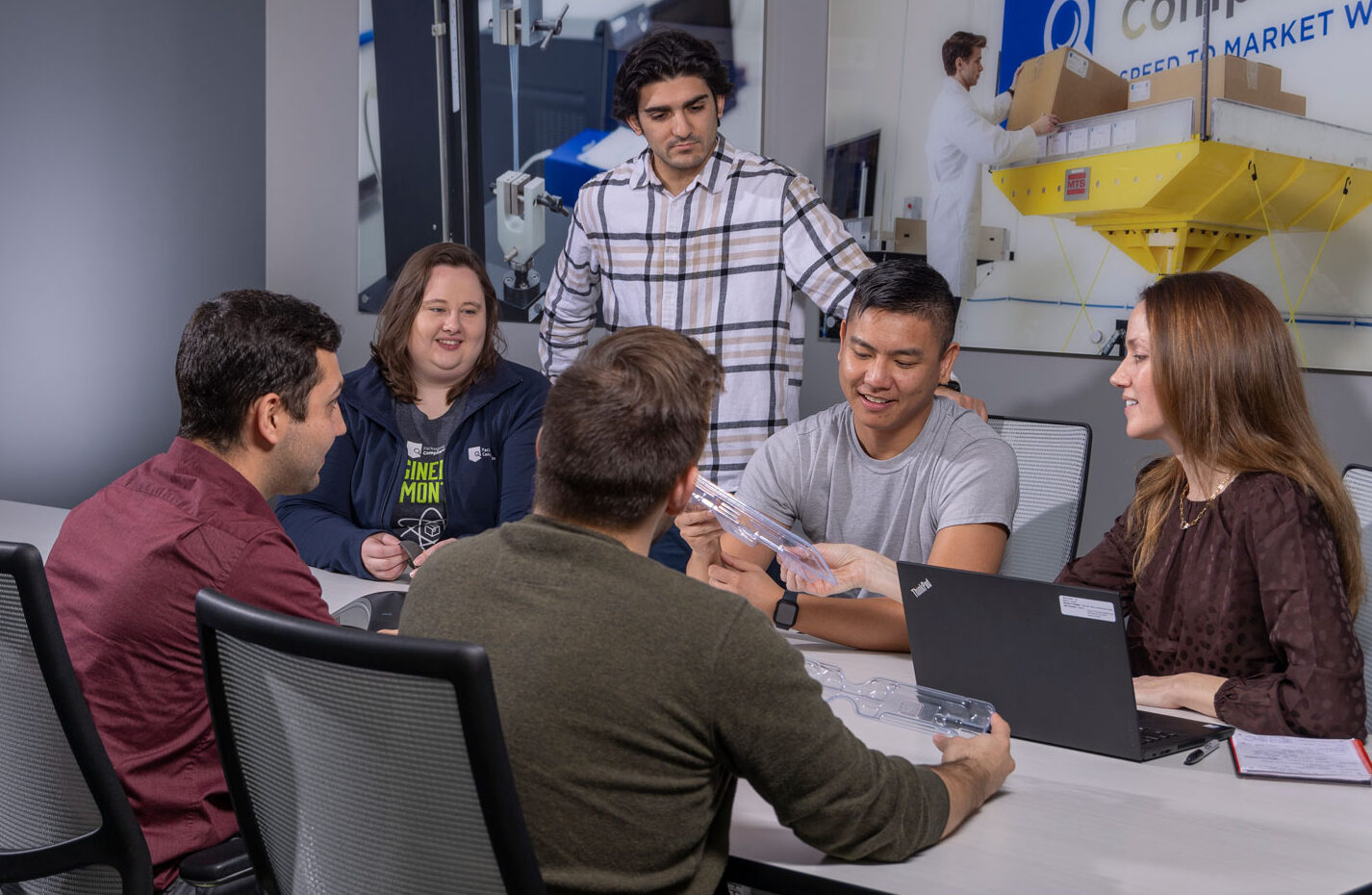