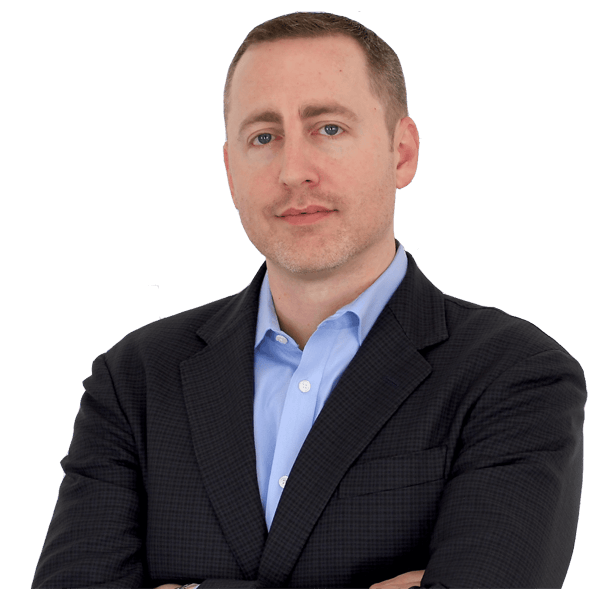
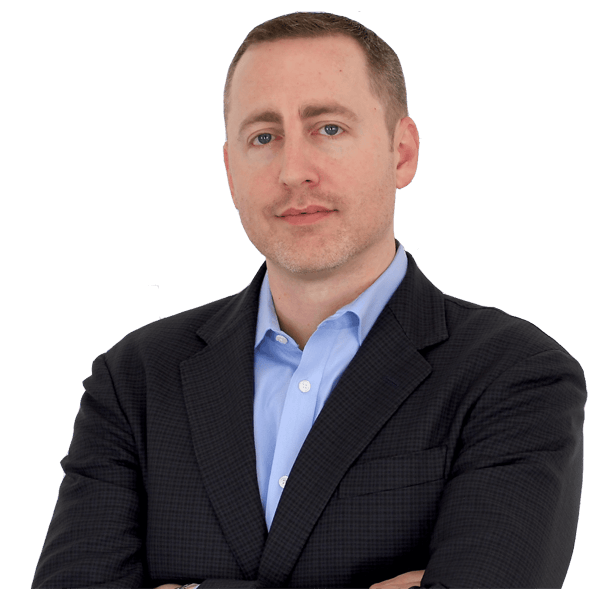
When you think of an engineer, what comes to mind? A quiet, introverted problem-solver? Have you heard the joke about the difference between an extroverted one versus an introverted one? The latter looks at your shoes when they’re talking.
All joking aside, engineering is a profession that requires attention to detail and an appreciation for processes and procedures. The most successful engineers know that adhering to quality standards is the pathway to business success. In the medical device packaging industry, adhering to standards is what we do.
Sometimes, it seems that we overlook the people side of engineering. And according to Ryan Ott, PCL’s Sr. Director of Quality and Principal Packaging Engineer, packaging is engineering with personality. “It takes a lot of teamwork and building good relationships to develop good processes,” he says.
The medical device packaging industry is all about quality and regulatory compliance, certifications, and processes to keep patients safe. Quality touches everything and requires significant employee interactions. “We’re not just pointing out mistakes,” he says. “Our approach is more centered on creating conversations that result in better processes.”
Ryan has worked hard to develop a people-centered culture of quality, which pays off with improved employee morale and performance. “I wanted people to understand the processes, and why those processes are important. Oftentimes regulatory requirements or equipment limitations may force engineers’ hand during the decision-making process, but I always like to have employee input to make sure the processes are efficient and effective.”
When Ryan worked as a line operator at a furniture factory after high school, he noticed that the engineers didn’t seek input from the operators when they created new processes. He didn’t recognize it as a lesson at the time. “Now I want to make sure that I talk to employees when I’m developing a process that affects their day-to-day work. We walk through the instructions together, which improves both the process and their attitudes about work.”
“When we write processes, we think about the most inexperienced people we know. And then we write for someone who has even less experience,” he says, “like it’s their first day on the job. Because we focus on so many details and get employees involved, we also build good relationships so they’re more comfortable coming to me with questions.”
Today, Ryan gives a lot of professional development advice and mentoring to employees. He helps them focus on their careers, shows them how to develop a career path, and helps them gain experience across different departments. He recently helped a colleague, think through their interests to expand their opportunities into a new role coordinating activities between departments and PCL. “We’re very good about hiring and helping them develop into leaders in the industry,” he says. “We like to show them how they are part of something bigger than they might think.”
“People like to work here for a couple of reasons. First, we’re all cool, so they want to work with the people they like to work with,” he jokes. “Seriously, people don’t want to dread working with people they don’t like. And since we have great people across the company, I think it means we’re doing something right.”
“Ensuring standards for quality is what we do,” says Ryan, “but the way you meet those compliance requirements should be a positive experience for employees. And that’s what good leadership is, for the company to surround the employees with not just the processes, but also the environment where they can succeed. Fundamentally, you’re going to have smarter and more satisfied employees, and that impacts client satisfaction all over the board. It’s a business philosophy that creates a better bottom line outcome.”