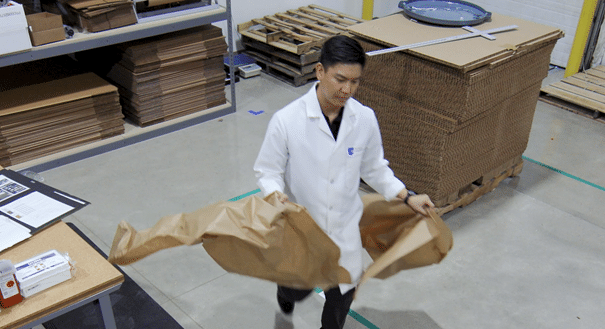
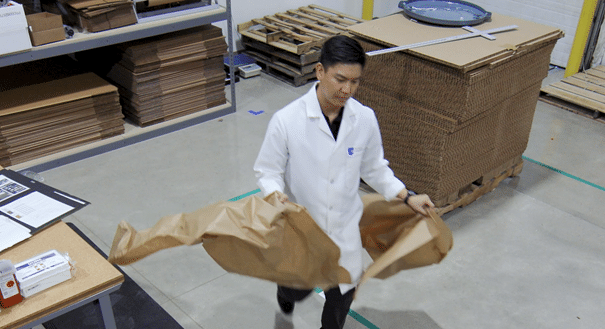
Often, clients ask how they should send their samples to the lab so they can be properly tested. For this, we recommend overpacking their samples to ensure they are protected from possible damage that could be incurred during transit to the lab. In this blog, we explain how to properly overpack a box with your samples.
The first step in overpacking is choosing how much Kraft paper dunnage you will need.
Next, Distribute the dunnage evenly to occupy the extra space inside an overpack shipper.
Make sure you have enough packing material to protect the contents by planning space on the bottom and top of the overpack container. Once the box is in the overpack shipper make sure the sides are cushioned with dunnage. If you have multiple boxes in one shipper, be sure to put dunnage between the boxes.
With the box securely packed, you are ready to ship your samples so we can get to work on validating the packaging.
Are you ready to work with PCL to validate your medical device packaging? Contact us today to set up a discovery meeting!