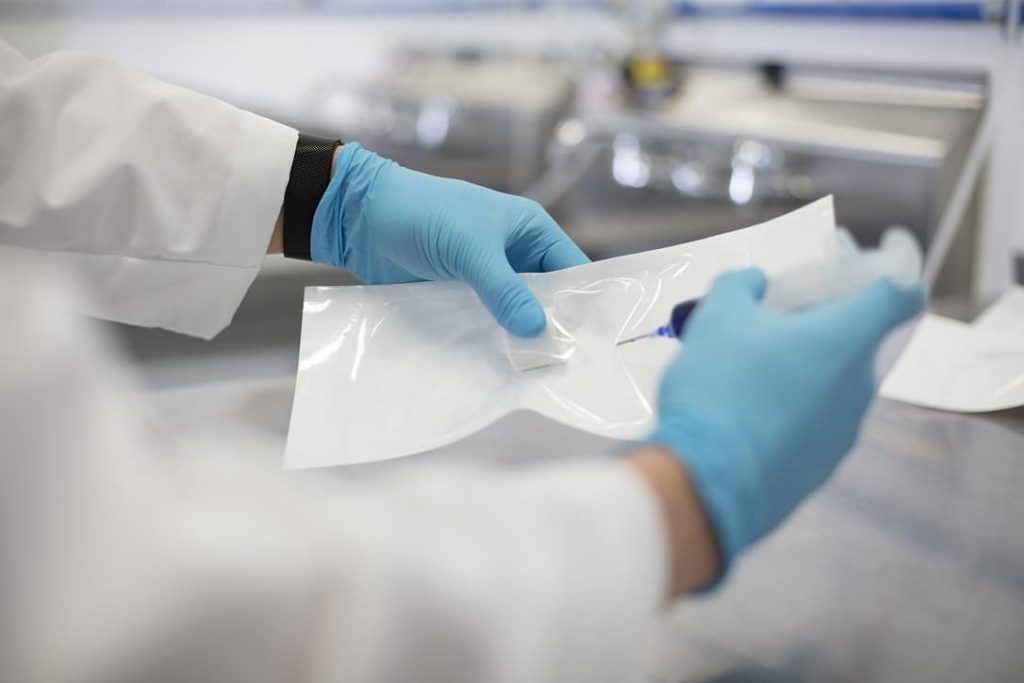
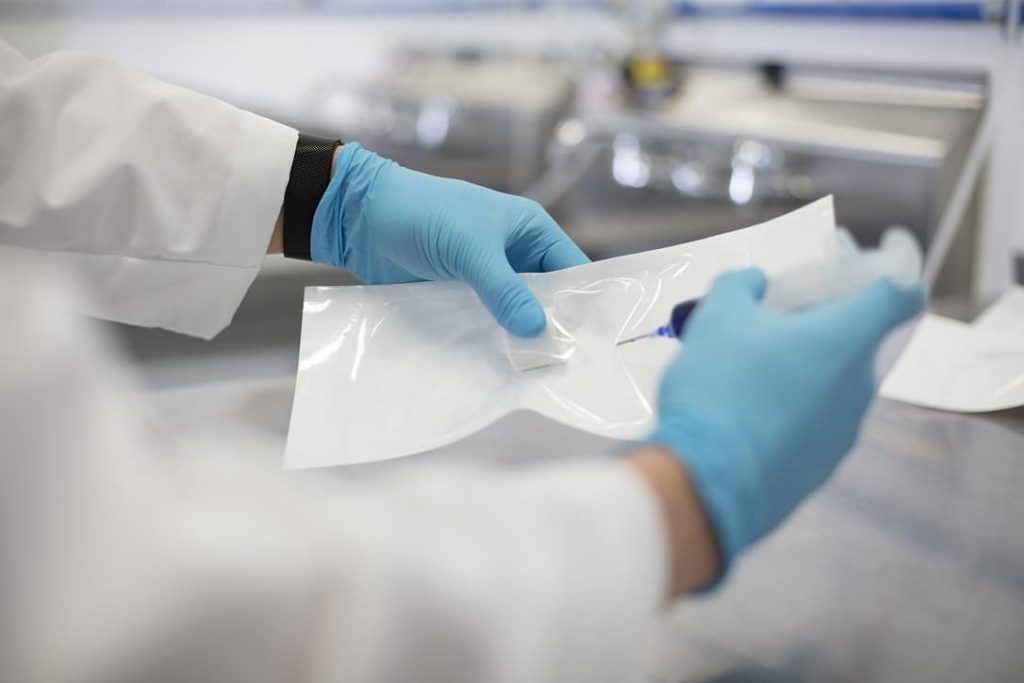
The stakes are high for medical device manufacturers to launch projects across the globe. Packaging validation standards vary depending on what country you live in, which can mean significant delays in getting products to market for small to medium medical device manufacturers. Ryan Erickson, PCL co-founder and Vice President of Packaging Engineering, recently sat down with European packaging consultant and testing expert Beate Seidl from PAConsult Meditec to compare testing standards.
Beate’s experience spans more than 16 years of conducting medical device package testing in Germany. She previously worked as a laboratory manager and has developed specialized expertise in packaging validation, including sterilization validation and biosafety.
Packaging Validation Approval Processes Overview
It is important to understand how medical device package designs are approved in both the United States and European Union before we review their similarities and differences.
In the US, the safety and suitability of medical device packaging are considered by the Food and Drug Administration’s (FDA) premarket approval process. ISO 11607 is the international standard that outlines the requirements for sterilized medical device packaging.
Medical devices sold in the EU must meet the EU Medical Device Regulation (MDR) which was approved in April 2017. Devices must conform to MDR regulations before they can be placed on the market. Manufacturers must gain approval from Notified Bodies (NBs) who certify that the products meet MDR requirements.
NBs are organizations designated by a member state to assess the conformity of certain products before being placed on the market. These bodies are entitled to carry out tasks related to conformity assessment procedures set out in the applicable legislation when the intervention of a third party is required. For more information about guidance documents, forms, approved notified bodies, and other important information, please check out https://ec.europa.eu/health/medical-devices-topics-interest/notified-bodies_en.
Also, the EU requires the CE (French for “Conformite Europeenne”) mark for products manufactured anywhere in the world and sold in the European Economic Area (EEA). The CE mark signifies that products have been assessed to meet high safety, health, and environmental protection requirements. Medical devices manufactured in the US must carry the CE mark when sold in the EU. The EU recognizes ISO 11607 standards, as well, and uses NBs to approve package testing validation. There are no CE mark grandfathering allowances prior to MDR, and all products must be reverified to receive the new CE mark.
Similarities in European & US Testing Standards
Both the EU and FDA recognize ISO 11607, says Ryan. “ISO 11607 is a requirement for sterile barrier packaging, and it’s harmonized across the US and EU markets, so we have commonality around that standard. When we meet 11607 in the US for sterile packaging, we expect to meet requirements to achieve the CE mark, at least as far as sterile barrier integrity and sterile packaging validation goes. ISO 11607 looks at the product-packaging system’s safety and effectiveness through the hazards of sterilization, distribution, and storage, as well as the manufacturing environment.”
Another similarity is that the two systems recognize the Class 1, 2, and 3 distinctions, which is a progressive order of risk associated with the product. Class 1 are low-risk products used externally to the body, like wound care or dressings. At the other end, are Class 3 products, which are internal to the body, such as implants, says Ryan.
Packaging validation requirements are the same for sealer, transit, and shelf-life to meet both FDA and MDR requirements, according to Beate and Ryan.
Differences in European & US Testing Standards
EU NBs provide approval that the testing validation confirms with regulations, so medical devices can achieve the required CE mark. One challenge is that the interpretation of the standards varies from country to country, and from auditor to auditor, which often makes it challenging to anticipate whether packages will meet MDR requirements.
In the U.S., the FDA is the regulatory agency that enforces testing validation for medical device packaging and works with third-party organizations that are accredited to do auditing and compliance according to established standards. In essence, the FDA is a NB according to EU requirements, but their approval is not recognized, and devices must be approved by local NBs. Even though the FDA reports indicate the packaging is compliant and meets ISO 11607, the standard for device packaging, it still needs to meet EU NB approval.
Testing laboratories do not certify packaging, says Beate. “We do testing, create reports, and our medical device clients provide the technical documentation to show conformity to the ISO11607 standard. You can take a report from the US or EU accredited lab, and if it meets ISO 11607, you can use it for an application to the US, EU, or even Asia. But the non-written interpretation requirements are different between the US and the EU. Sometimes the manufacturer will get deficiencies because the NB has special protections or requirements. This is the difficult thing here.”
“The more we know about the differences between the ISO 11607 and the NB requirements, the more we can help our clients understand that they need to have the information. The testing work is not any different,” she says.
“We tend to make more conservative choices,” says Ryan. “If we know that the validation program is destined for the CE mark, we know there will be more scrutiny during the validation process than what might otherwise be encountered in the US. It will be going through a more thorough audit and review phase. We work with all the requirements, and just make more conservative choices.”
Also, while the EU accepts a lot of American Society for Testing and Materials (ASTM) guidelines, the EU NB also has additional requirements from EN standards. “I don’t think the FDA is interested in these,” says Beate, “but we have to do them for the CE mark.”
“There are standards in the EU that are more related to how we meet the ASTM standard, but it’s a different European organization that is responsible for developing the content, so they may come out a little bit differently,” says Ryan. “It may not be an exact one-to-one comparison, so we have those particulars to be aware of as well.”
One of the differences in shelf-life testing is that NBs are looking at real-time aging parameters, which Beate has not seen in FDA special requirements. “It is a little more difficult right now in Europe,” she says. “Recently, we had a client that had deficiencies from his NBs, and he was asked for the stability validation. They wanted to see real-time aging according to the climatic zone but it’s expensive to have this in storage for four or five years. They wanted to know if the real-time aging was done for Asia which could have been 30 degrees Celsius and 75 percent humidity. I have never heard that the FDA is expecting such real-time aging parameters.”
PCL performs real-time aging in their warehouse under controlled human-ambient conditions, says Ryan. “We hook up a chart recorder to monitor temperature and humidity and maintain that record over time. We don’t have any specific requirements that we impose unless we’re aware of the products having some special considerations that need to be accounted for. We use normal air conditioning for human comforts in a typical warehouse-type environment, with temperatures 20-25 Celsius, with seasonal ambient humidity.”
There is a distinction between package integrity and microbial barrier. The first is maintaining a sterile barrier as part of the package, so it doesn’t have rips, holes, tears, or seals that are broken open, which could allow microorganisms to enter the packaging. A microbial barrier relates to the materials themselves.
“What we’re concerned about is whether a porous material like Tyvek, coated papers, or other nonwovens prevents microorganisms from passing through it,” says Ryan. “The same is true for a non-porous material, and we need to demonstrate that the material is indeed non-porous. There might be some micropores or air that could pass through, which would be the pathway for microorganisms.
“We lean on the material specification sheets we receive from our suppliers to furnish that type of information. We contact the sterile barrier suppliers and ask for the microbial barrier testing so they can provide evidence, such as a data sheet, that would show the microbial sphere formation. It sounds like in the EU that there may be some additional effort around the microbial barrier.”
“We do that, too,” says Beate, “and also for risk management. But then the question will come from the NBs to ask us to prove that this is not changing during shelf life, for example. So, a lot of the NBs or auditors expect after five years of aging that you prove again the microbial barrier properties of the material.”
“We encounter a lot of customers who are launching products in both the US and EU,” says Ryan. “Some are working on getting into either one market or the other at a given time and can launch first in the EU or in the US. We are not always given information about where the launch is going. If we know that the product is being launched in the EU and they will be seeking the CE mark, then we will make more conservative choices. It’s good to be aware of issues, such as microbial barriers, so we can be better prepared for validation reporting in the EU.
In 2017, the medical device regulation (MDR) changed for all EU medical devices, and the industry is still in a state of transition. Many devices that met old documentation must be redone to meet the new MDR standards. There are more expectations from NB, so many packaging validation firms are revalidating devices to meet the new MDR requirements. Device manufacturers now must prove that packaging and the product are able to withstand some transportation parameters, hazards, and storage for both sterile and non-sterile products, says Beate.
By and large, the packaging validation has not changed significantly to meet the new MDR standards, says Ryan, especially since manufacturers meet internationally accepted ISO standards. One significant change has been in considering the human factors and usability evaluations. There are also new requirements for labeling, including whether or not there is a sterile barrier included in the packaging.
“A lot of clients are struggling with that,” says Beate. “They need to identify if a pouch is part of the sterile barrier or part of the protective packaging. Another concern of the NBs is the readability of the label. We are checking both the labels and the instruction for use, including destructibility and aging.”
Summary
While the 21st century is the global marketplace, not all medical device manufacturing approval requirements and processes are the same. Devices sold in the EU must receive the CE mark, which is approved by NBs that have some standards that are the same as those in the US, and others that are more stringent. Differences are many and include the level of scrutiny, testing processes, and meeting more stringent regulations.
US medical device manufacturers have a lot riding on gaining approval for launching products in the EU. When they understand the nuances and schedules for meeting detailed requirements, they are likely to have products approved faster so they can generate revenue as their product line expands to serve healthcare facilities, doctors, and patients in the EU.