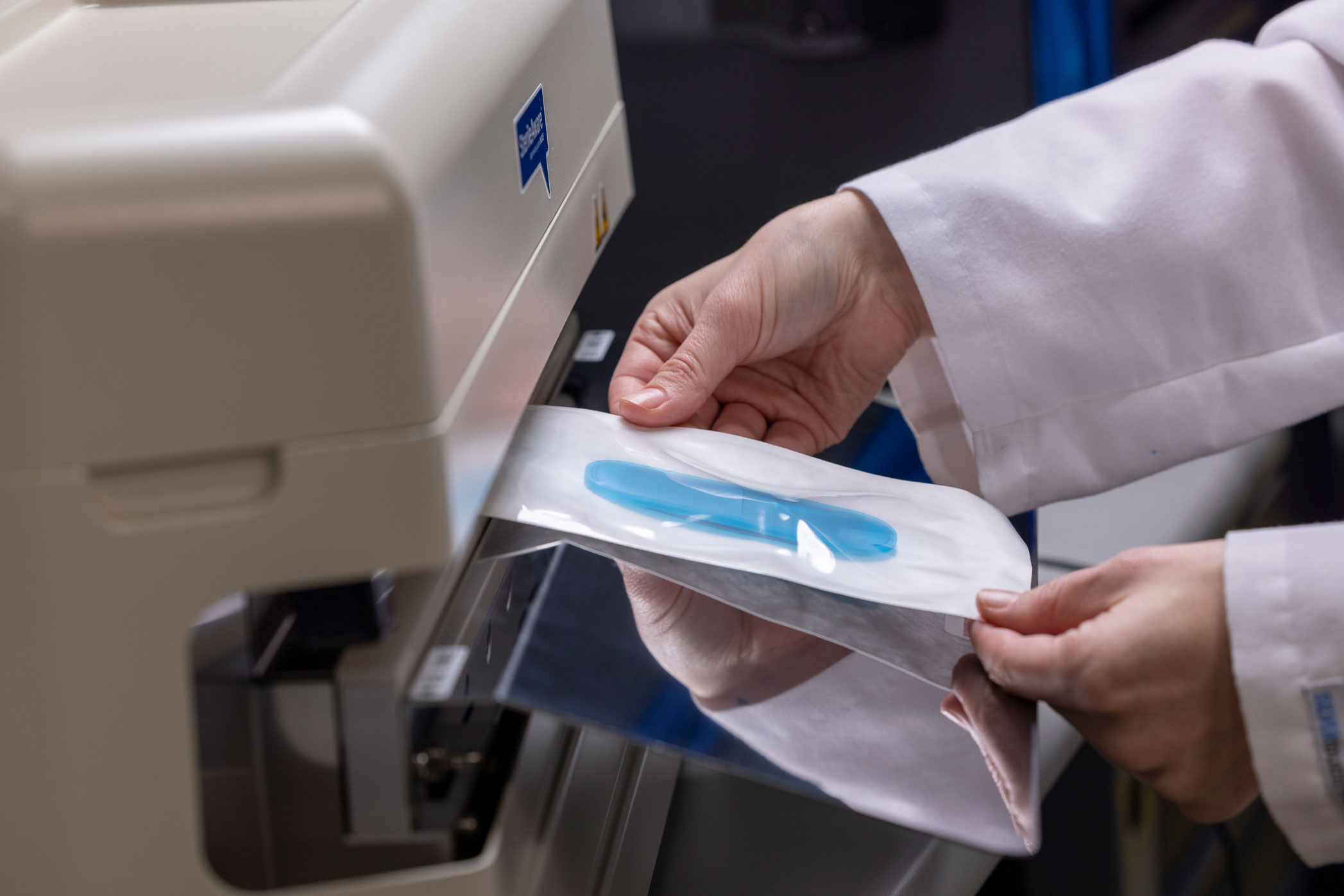
Turnkey Sealer Validation
ISO11607 Part 2 requires that sterile barrier packaging processes, including forming & sealing, be validated through a three-step process:
- Installation Qualification (IQ)
- Operational Qualification (OQ)
- Performance Qualification (PQ)
Let our engineers assist you in managing this effort from start to finish. We will author all the relevant protocols, visit your facility to execute the validation work for your sterile packaging sealing equipment, train your employees in the appropriate procedures, coordinate and perform the relevant sterile barrier testing, and issue reports and work instructions.
Step 1: Installation Qualification – Laying the Foundation
As defined in ISO 11607-2 (Section 3.5), IQ is the “process of establishing by objective evidence that all key aspects of the process equipment and ancillary system installation comply with the approved specification.
At a high level, the IQ checklist is:
Check for correct equipment specifications (model, size, configuration)
Verify appropriate environmental conditions (temperature, humidity, cleanroom requirements)
Check utilities (air pressure, electrical, calibration, etc.)
Review maintenance and calibration records to confirm accuracy
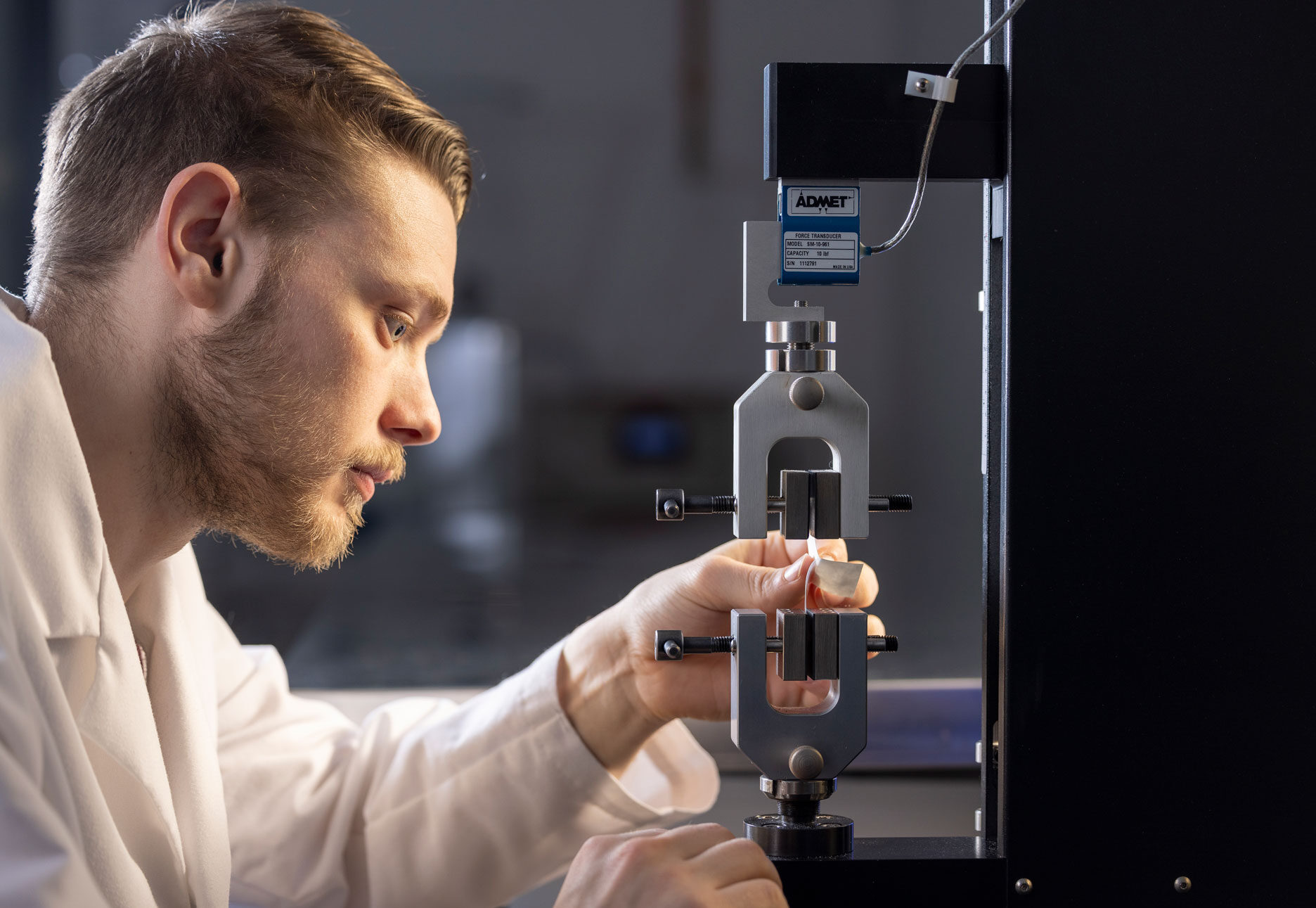
Step 2: Design of Experiments (DOE)
The DOE is possibly the most important step in sealing validation, but it is not explicitly captured in ISO 11607-2. However, at PCL, we perform a DOE for every sealing validation that we execute. Identifying the correct sealing window ensures that downstream validations go smoothly, preventing unnecessary rework. The steps included in a DOE are:
- Edge of Failure Study
- Range Finding Exercise
- Visual Scoring
- Seal Strength Characterization Plot
- Establishing the Sealing Process Window
Step 3: Operational Qualification – Testing the Limits
During your OQ, you’re confirming that the equipment produces good seals even at its worst-case limits. This can prevent unexpected failures during production
Testing at this step includes:
Sealing at the lowest and highest parameters
Simulating real-world equipment fluctuations
Testing for integrity: Visual Inspection (ASTM F1886), Seal Width (ASTM F2203) , Dye Leak Testing(ASTM F1929 or F3039), Aseptic Opening (Per ISO 11607), Seal Strength (ASTM F88)
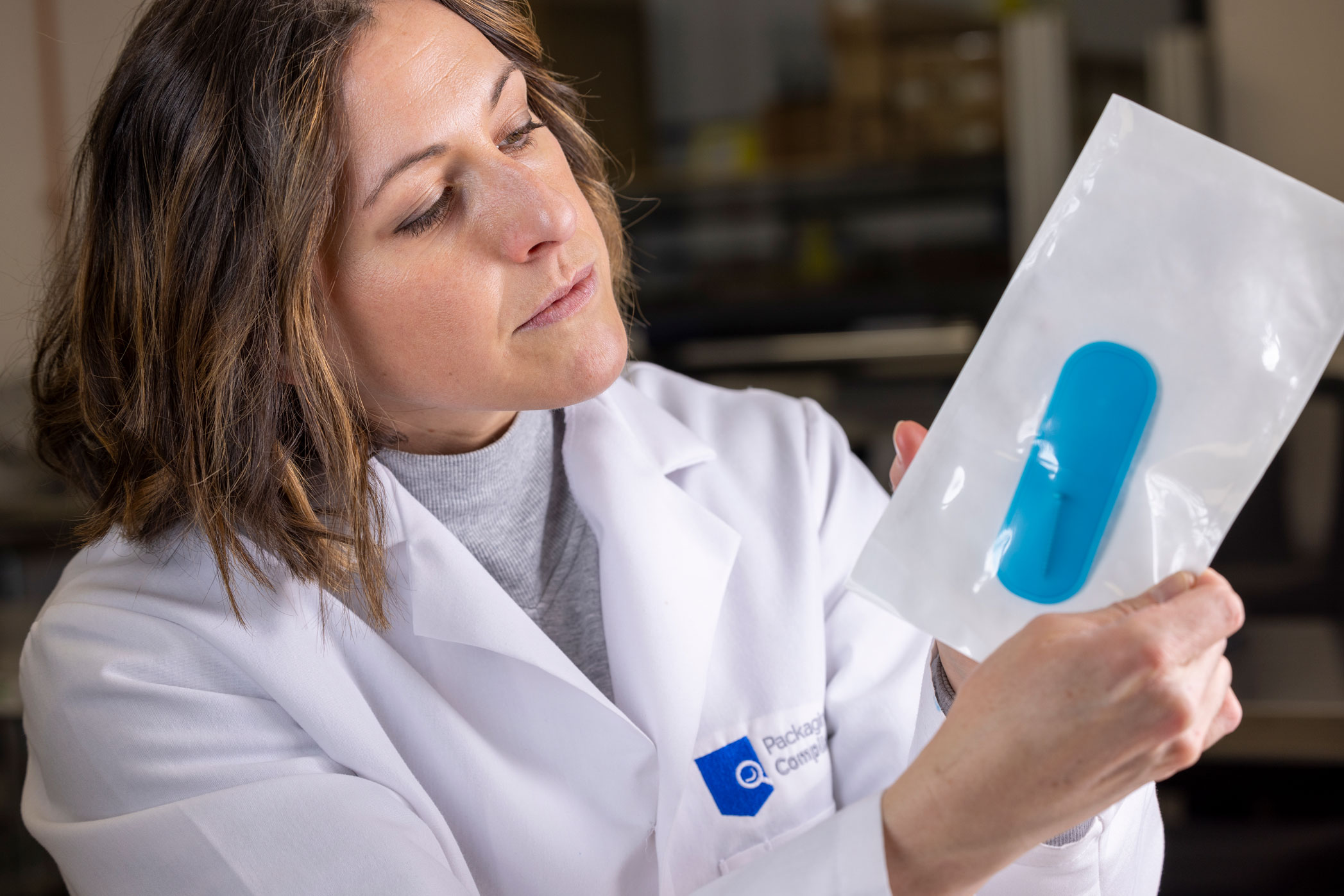
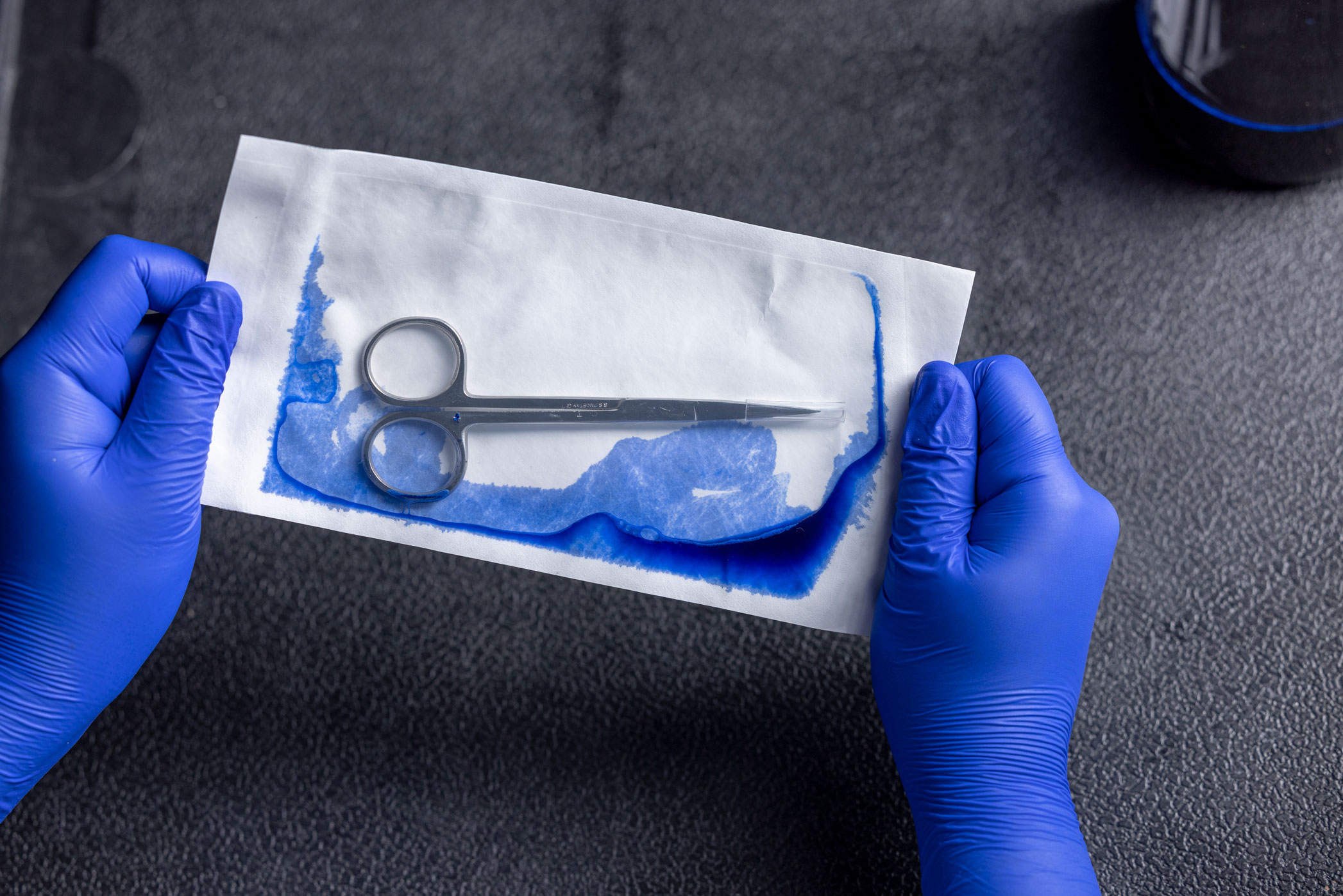
Step 4: Performance Qualification – Confirming Stability
Performing a PQ ensures your sealing process is stable and capable under routine conditions.
Testing at this stage includes:
- Sealing three production lots at nominal parameters.
- Including product to evaluate how device size and weight impacts the seal.
- Performing the same testing as in OQ to confirm seal integrity.
Sealer Validation Deliverables
When you work with PCL for your sealer validation you will receive the following deliverables:
Authorship of protocols
Memorandum of seal characterization and range finding memo
Detailed work instructions for equipment and packaging
On-site client training
IQ/OQ/PQ validation reports
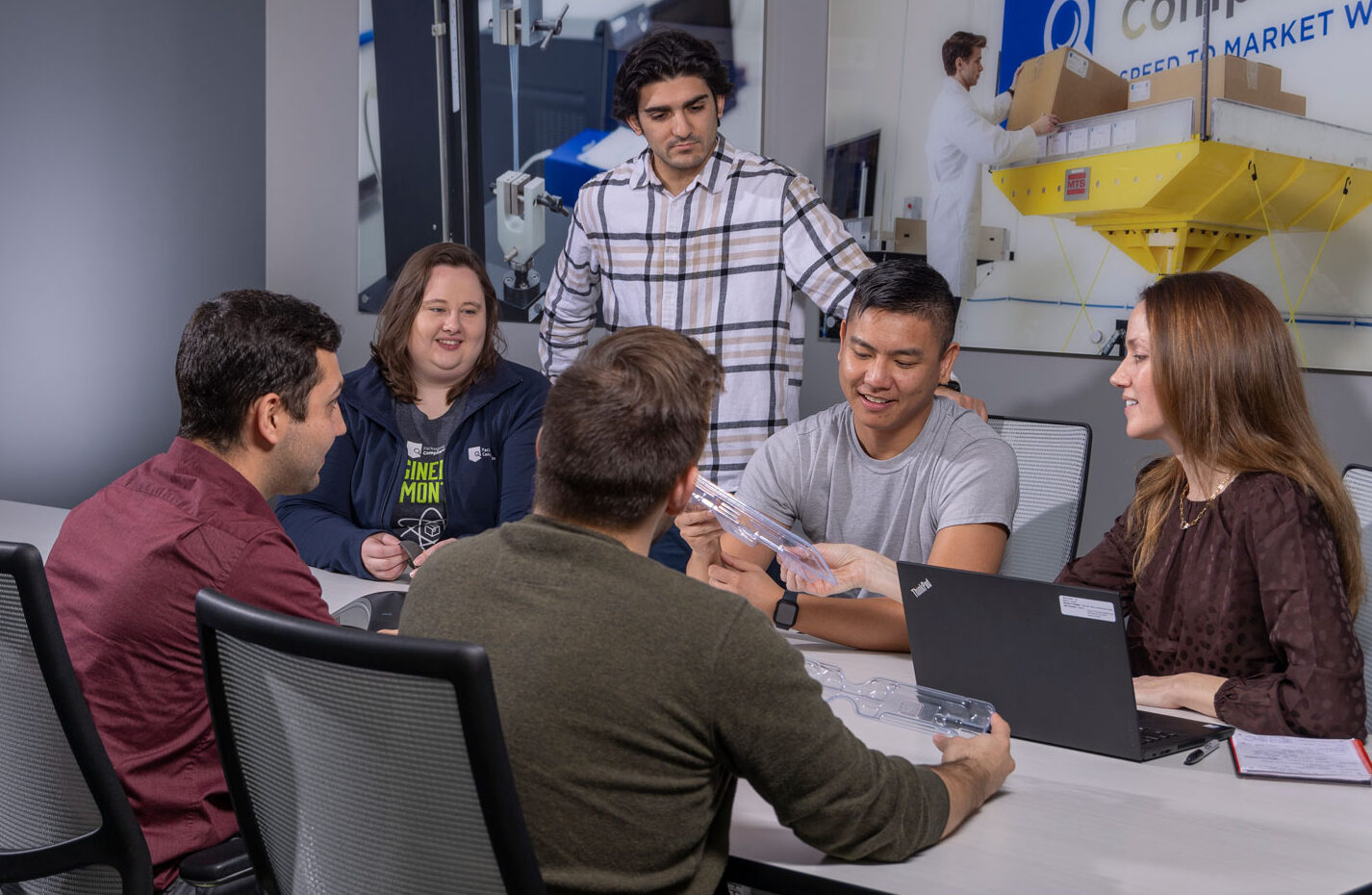
Let's Start Your Sealer Validation
To get started on your medical device sealer validation, please provide your contact information and select an option that fits your needs or select 'I Need Guidance' if you require some assistance.
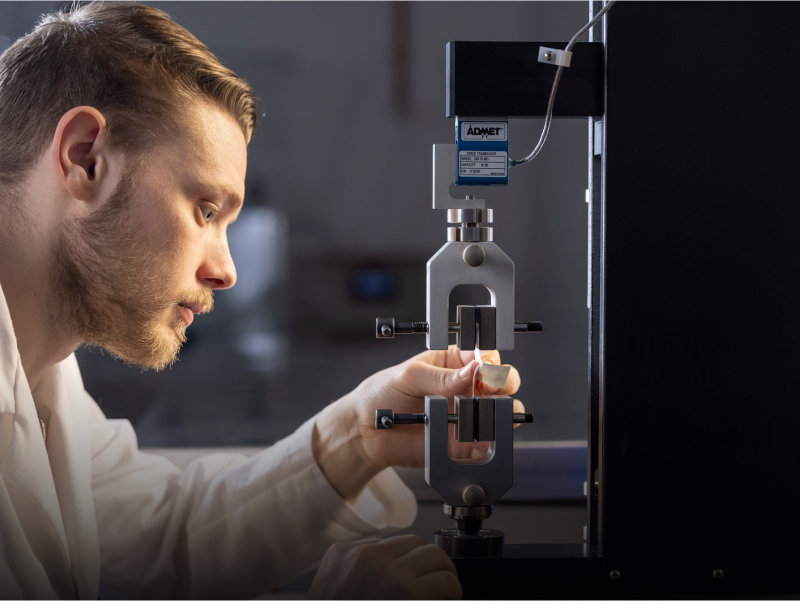