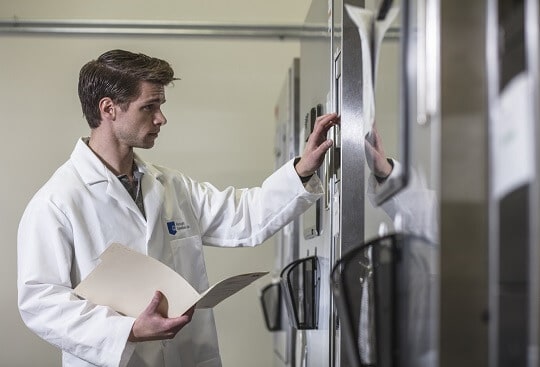
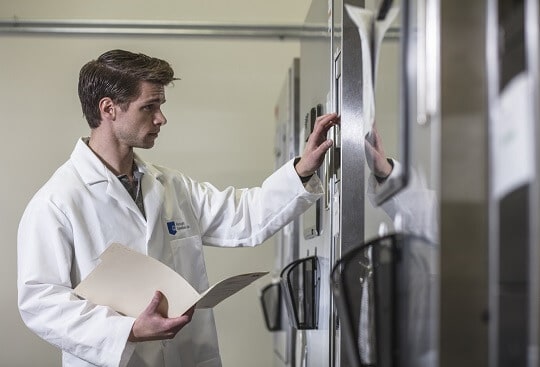
“Since joining the healthcare packaging industry, I view packaging and shipping containers in a new light. Before, I never considered the different kinds of tests that packaging must endure for it to arrive at my doorstep unscathed. What bamboozled me the most was my on-the-go meal kits packaging from Blue Apron. How is this ice pack still frozen? How is this meat still frozen? Is this wizardry? How come the stinkin’ ice pack in my lunch box doesn’t keep my food this cold??
All my questions have now been answered and I have learned that it is not wizardry that makes this possible, but rather, cold chain qualification.
Cold chain qualification is a great way to validate packaging for home delivered food products like my Blue Apron example. In fact, it is a must have when developing packaging for sensitive healthcare products that require a temperature-controlled environment.”
- Cassie Peterson, Marketing Manager
In this blog, we will explain further what cold chain qualification is and how it is performed.
What is Cold Chain Qualification?
Cold chain qualification, sometimes referred to as thermal cold storage validation or thermal packaging qualification, is a means for manufacturers to validate their thermal packaging system’s ability to distribute and deliver products to end users at acceptable temperatures. Cold chain qualification simulates what thermal packaging systems feel throughout their distribution from a temperature perspective. From both the products standpoint… and the packaging.
With cold chain qualification, we are trying to simulate the entire process of a thermal packaging systems supply chain. In layman’s terms, think of cold chain distribution in four phases: 1) Storage, 2) Packing Out Packages, 3) Distribution, and 4) Use.
Storage
So, what should you consider when discussing simulating storage environments? Let’s take a step back and take an inventory of what a thermal packaging system entails. What is the product? Are there multiple components to the product? Are there temperature control components like gel packs or dry ice? And finally, packaging, how many packaging components are there within each system?
When considering the initial storage conditions of all components of a thermal packaging system, it is important to understand the parameters of their storage environment: temperature, humidity, and minimum storage duration of each component.
For example, if you are validating a thermal packaging system for cold chain distribution and you intend to ship product with frozen gel packs, the gel backs better be frozen before pack out during testing to properly capture the storage environment.
Packing Out Packages
Next up – packing out thermal packaging systems. Once you get to the pack out phase, you must consider how long a company’s standard operation procedures allow them to take to pack out. If products cannot be out of their storage environment for less than fifteen minutes, then each packaging system must be packed out within fifteen minutes.
In our experience, we have seen requirements as little as one minute and as long as one hour for pack out duration.
It is critical to consider the pack out process when developing a test plan for cold chain packaging validation. How much does the dwell time of product and packaging components in a pack out environment affect a thermal packaging system’s ability to distribute and deliver product with acceptable temperatures? The answer is – it depends on a lot of factors including the thermal inertia of each component. At the end of the day, that is why it is important to simulate the pack out process as closely to intended processes as possible.
KEEP IN MIND: To record the temperature of the thermal packaging system during testing, thermocouples will be installed during the simulated pack out process.
Distribution and Use
Once samples are packed up the next step is to simulate the environmental conditions of the thermal packaging system’s supply chain. The thermocouple packages are placed in a conditioning chamber and subjected to climatic conditioning profiles. Widely industry recognized standards are ISTA 7D, ISTA 7E and ASTM D4332.
At the end of the day, you analyze the data to see if it maintained acceptable temperatures through the selected climatic conditioning profile.
The Climate Conditioning Standards PCL Can Use for Cold Chain Qualification
Cold chain qualification simulates what thermal packaging systems feel throughout their distribution channel from a temperature perspective. The intent of this test method is to demonstrate the ability of thermal packaging systems to maintain product payload temperatures at specified temperatures for a specific duration of time.
There are a few different ways you can go about considering climatic conditioning profiles. The healthcare packaging industry uses ASTM D4332 (Standard Practice for Conditioning Containers, Packages, or Packaging Components for Testing), ISTA 7D (Temperature Test for Transport Packaging) and ISTA 7E (Testing Standard for Thermal Transport Packaging Used in Parcel Delivery System Shipment).
ASTM D4332 is a widely industry recognized climatic conditioning standard that prescribes different historically accepted profiles based on standard regional conditions. Examples of this are Extreme Cold (low temp, low humidity), Desert (high temp, low humidity), and Tropic (high temp, high humidity).
ISTA 7D prescribes climatic conditioning profiles within the framework of anticipated environmental conditions experienced during domestic and international air freight shipments within the summer and winter time seasons. 7D also refers to hot shipping/hot receiving and cold shipping/cold receiving, which refers to the environment you are packing out, shipping, and receiving in.
ISTA 7E is a process standard that outlines a procedure to validate thermal packaging systems. The process includes different protocols that entail thermal (cold chain) qualification, physical qualification (temperature monitoring in tandem with distribution simulation) and thermal verification testing. With physical qualifications, you are evaluating the effects of the hazard modes of distribution on the package’s ability to maintain acceptable temperatures through standards like ASTM D4169 and ISTA 3A.
Industries that require Cold Chain Qualification
The two main industries that require cold chain qualification are Biologics/Pharmaceuticals and Food.
Biologics/Pharmaceuticals
Biologics are drugs that are derived from humans, animals, or contains components from living organisms. Biologic products may include drugs, vaccines, blood, tissue, and more. Pharmaceuticals typically require tight windows of thermal parameters which is why cold chain qualification is required.
When the vaccine for COVID-19 is developed and it passes clinical trials, the next step is to validate its cold storage packaging per the usual ISO 11607 test methods. In the case that a vaccine for COVID-19 is temperature sensitive, cold chain qualification testing will assure the manufacturers that the vaccine should not be affected by anticipated environmental conditions throughout the products supply chain.
Food
Think ‘easy to go’ meal kits like HelloFresh and Blue Apron. Referring back to my real life example, any food that requires refrigeration/freezing to stay good will require cold chain qualification to ensure the temperature control materials will stay cold during the pack out, distribution cycle, and on a porch for a few hours before being transferred to the end users freezer or refrigerator.
PCL recently announced their 5th building expansion will take place this Summer. The expansion will include an additional 5,000 square feet that will include additional space for the office and validation lab. The lab portion of the expansion will include space that is dedicated to cold chain qualification.
Questions about cold chain testing and qualification or cold chain packaging systems?
Click here to Contact Us today!