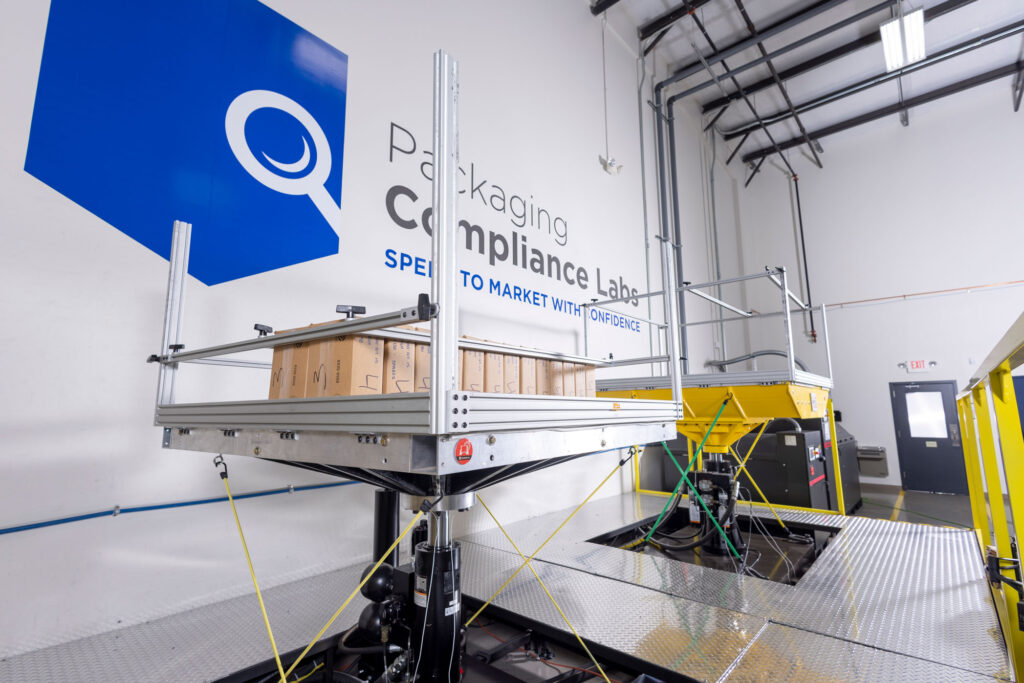
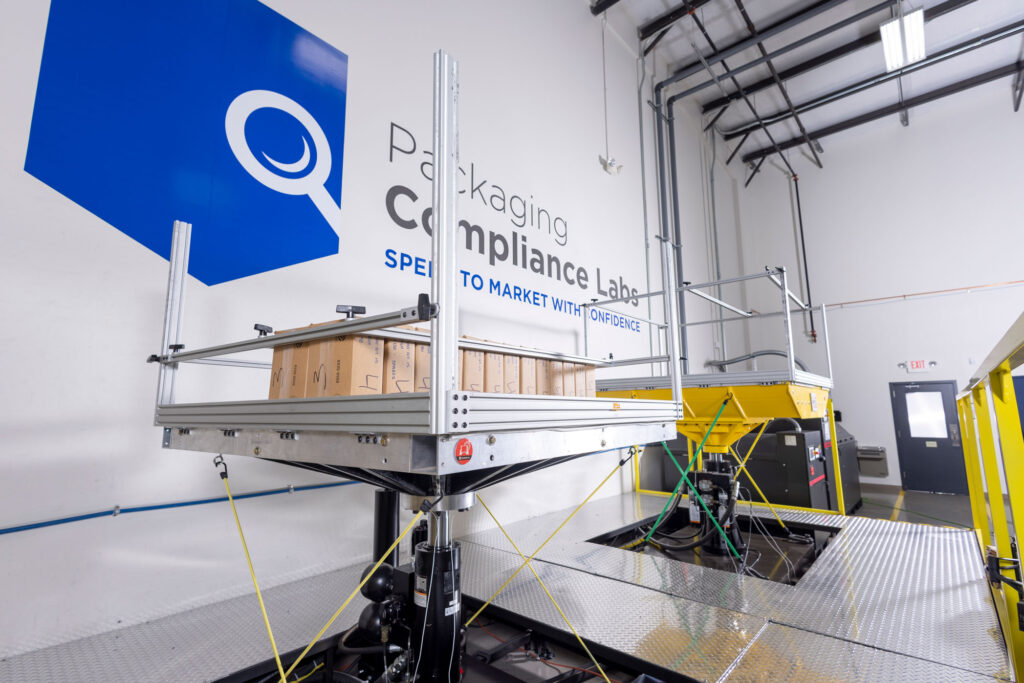
In the world of medical device packaging, determining the worst-case scenario is a strategic process that balances risks and costs. If you intend on shipping your product via both small parcel and palletized shipments, do you have to perform a transit validation on both? Find out what our packaging experts say below!
The Role of ISO 11607
ISO 11607 plays a pivotal role in guiding this decision-making process. Instead of testing every product individually, the standard allows for a more pragmatic approach. It encourages the identification of product families, enabling the testing of representative groups rather than the exhaustive testing of every product variant.
Once you’ve narrowed down your product families, you move on to your worst-case packaging configuration.
Defining the Worst Case
Performance Testing (transit studies) are a crucial and required aspect of packaging development. Determining the worst-case configuration within a shipper is essential to adequately challenge the package system. While conventional wisdom often points to testing the largest, heaviest configuration, surprises can occur. Feasibility testing becomes a valuable tool in discerning whether the largest or smallest device poses the worst-case scenario.
Although both shipping options are common, the small parcel environment is typically considered the worst case. Small parcel shipping introduces a level of unpredictability that palletized shipping tends to avoid. The ability for unknown elements to impact a shipper during transit, such as inadvertent drops, lack of a fixed orientation, or items placed on top of it in a delivery truck, creates challenges that must be considered and challenged during performance testing.
While palletized shipping offers more stability, it is not without its own set of challenges. ISO 11607 emphasizes that packaging shall provide adequate protection to all sterile barrier systems and the sterile contents through the hazards of handling, distribution, and storage. This includes scenarios where a pallet may slam into another or slide around the back of a truck. Strategies such as using no-stack pallet cones to prevent double stacking help mitigate risks. It’s important to note that unforeseen circumstances, such as a forklift piercing through packaging, are considered beyond the expected hazards that can be routinely experienced in the distribution environment.
The decision to ship medical devices in individual boxes or palletized form requires a thoughtful approach that balances risk and cost. ISO 11607 provides a framework for identifying worst-case scenarios within product families, ensuring that packaging survives the rigors of the distribution environment. Whether it’s the unpredictability of small parcel shipping or the challenges of palletized shipping, the key lies in comprehensive testing that aligns with the unique characteristics of each shipping method.